Why use Anodized Aluminium Material?
The purpose of anodizing aluminum is to form a layer of alumina to protect the aluminum below it. Aluminum is a soft metal, anodizing is an electrochemical process, which can have metal surfaces such as aluminum with decorative, durability, and corrosion resistance. Aluminum oxide layers have higher corrosion resistance and wear resistance than aluminum itself. Anodized aluminum helps to improve the life, durability and aesthetics of the product, and other advantages.
Application of Anodized Aluminium
Anodized aluminum is used in a variety of consumption and commercial products and equipment. Anodized aluminum can be used in a variety of final products, for example:
Building outside, such as a storefront, window frame, mailbox, roof system
Refrigerator, dryer, coffee bubble, stove, television and microwave equipment and other electrical appliances
Equipment for food (display cabinet) and leisure industries (golf cart, boat and camping / fishing equipment), and
Daily supplies, such as clocks, fire extinguishers, solar panels, phones, photo frames and bathroom accessories.
Aluminum is well suited for anodizing, although other non-ferrous metals (such as magnesium and titanium) can also oxidize.
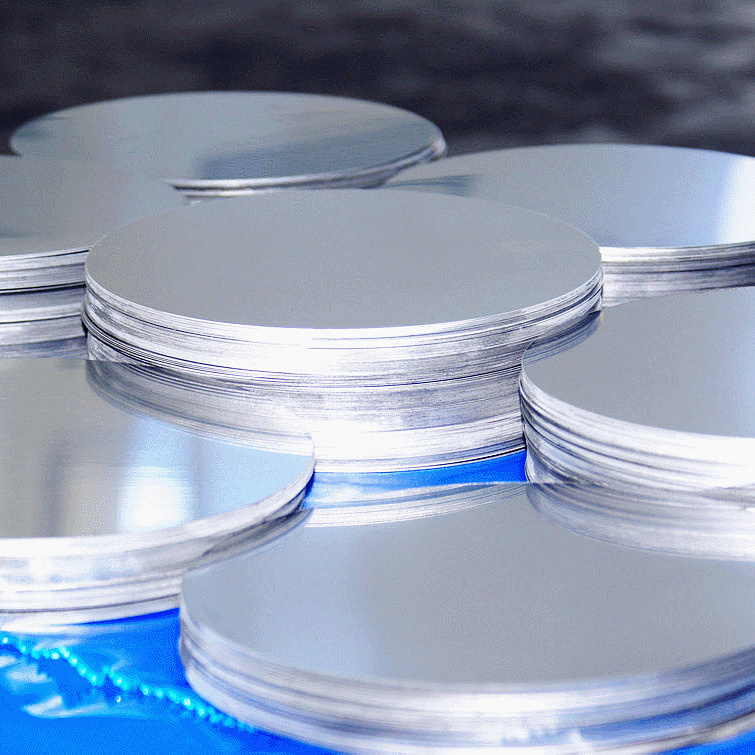
Four Types of Anodized
There are usually four methods for oxidizing aluminum anodic oxidation.
Sulfuric Acid Anodize. This is the most common method of oxidation of aluminum. It is especially suitable for applications that require hardness and wear resistance. However, in a place where the part is subjected to larger stress (eg, aircraft part), it is undesirable to have a corrosive acid residue.
Hard Anodized (Hardcoat). The hard coating anode oxidation is thicker, denser. Hard coatings are suitable for aluminum components that need to prevent extreme wear, abrasion and corrosion. It may also be valuable when enhanced electrical insulation and saving wear or misunderstanding.
Amodite oxidation of chromate (CAA). Chromate anodic oxidation can produce all the anode oxidation types of anode coatings. It is displayed as gray and absorbs less colors after dying. Therefore, it cannot be used for decorative decoration, but it can be contaminated as a non-reflective protective coating.
Boric-Sulfuric Acid Anodize (BSAA). BSAA is a substitute for chromic acid, mainly due to environmental, workers’ safety and health considerations. The adhesion of the coating is equal to or superior to chromic acid, and the process is more energy-efficient than chromium-based processes. It is usually found in a precision machining part, such as aircraft parts.
Benefits of Anodized Aluminum
When high-performance aluminum finishes are required, the anodization is very suitable. These are some advantages of the anodized aluminum:
Durability and cost efficiency: Most anodized products have a long service life. Their durability reduces maintenance costs and creates higher long-term value and significant economic advantages.
Color stability and aesthetics: The external anode coating is stable to ultraviolet rays, and it does not break or peel it, and it is easy to repeat. Anodic oxidation provides a variety of gloss and color selection, and minimizing or eliminating color changes. Unlike other finishes, the anodization can keep aluminum its metal appearance.
Easy to maintain. The anodized aluminum does not cause scar and wear due to manufacturing, processing, mounting, and frequent surface dirt and use. Mild cleaning usually restores its original appearance on the surface of the anodized surface.
Health and safety: Anodic oxidation is a safe process that is harmless to human health. Because the anodizing process is an increase in the oxide process, it is harmless and does not produce harmful or dangerous by-products.
Anodized Aluminum Supplier
Anodized aluminum has many advantages and applications. If you want to have an anodized aluminum material, you can contact LANREN Aluminium to support your project. We have the whole line to produce aluminum coil and aluminum circles and aluminum cookware, etc.