What’s the Aluminium Circle Sheet Application?
Aluminium circle sheets have become popular across various industries due to their lightweight, corrosion resistance and excellent formability. Cut from aluminium coils or sheets, these discs can be found in cookware, lighting, electronics and decorative applications such as cookware. In this article we will look into their manufacturing process, key applications and common alloys.
What’s the Aluminium Circle Sheet Manufacturing Process
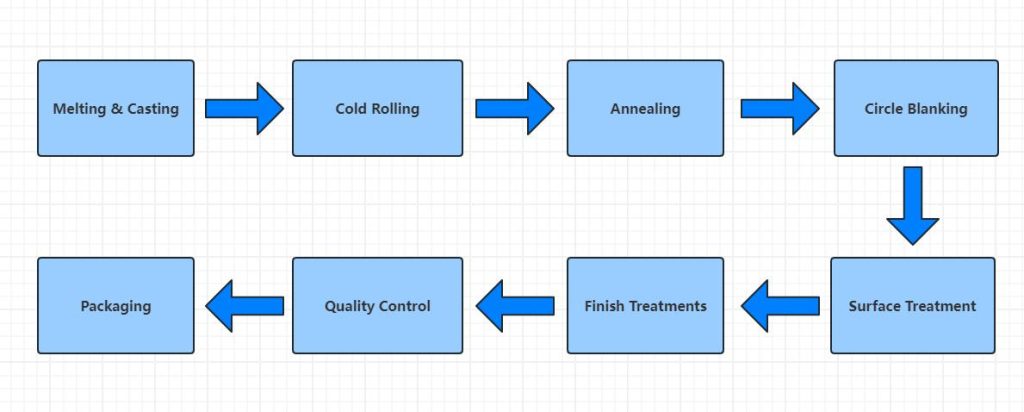
Aluminium circle sheet production involves an intricate multi-stage process designed to ensure optimal quality and performance:
- Melting & Casting: Aluminium ingots are melted down and cast using direct chill casting (DC), producing large slabs with uniform structures. After being heated up for hot rolling (heating + rolling), thinner strips (typically 2-10mm thick) can then be created for improved workability.
- Cold Rolling: Cold rolling occurs at room temperature to reduce thickness further while improving surface finish and mechanical properties, as well as surface finish quality and mechanical strength.
- Annealing: Annealing softens metal so deep-drawing applications such as cookware can take place more effectively.
- Circle Blanking: Precise hydraulic or mechanical punches create round discs of precise diameter tolerance (+/-0.1mm).
- Surface Treatment: After they’ve been cut out of sheets, precision punches use hydraulic or mechanical pressure to cut round discs into discs of precise dimensions (+/-0.1mm).
- Finish Treatments: Can include anodizing (for lighting use), coating (cookware applications), or polishing (decorative purposes).
- Quality Control: Before packing aluminium circles are tested for thickness uniformity, flatness and surface defects to ensure their quality meets industry requirements in terms of strength, corrosion resistance and formability across various applications. This comprehensive testing system guarantees they deliver on industry expectations in terms of strength, corrosion resistance and formability across applications.
What Are the Main Applications of Aluminium Circle Sheet
Aluminium circle sheets are among the most versatile metal materials, prized for their lightweight nature, excellent thermal conductivity, corrosion resistance, and ease of fabrication. These properties make them ideal for a wide range of industrial and consumer applications. Below, we explore the key uses of aluminium circles in detail.
Non-stick Coated Aluminium Circle for Cookware
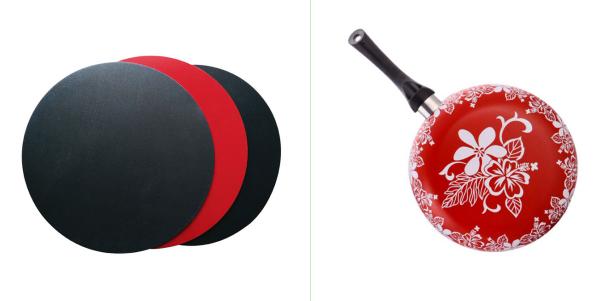
One of the primary uses for aluminium circle sheets is in producing cookware. Thanks to their excellent heat conductivity, Non-stick coated aluminium circle have long been employed in creating pots, pans, pressure cookers and baking trays made out of aluminium circles.
- Non-Stick Coatings: Modern cookware items often feature Teflon or ceramic non-stick coatings applied directly onto aluminium circles to prevent food from adhering and make cleaning simpler. This prevents food from sticking while making cleanup simpler.
- Even Heat Distribution: Aluminium ensures even heat distribution, eliminating hot spots which could burn food and prolonging cooking times.
- Lightweight yet Durable: Aluminium cookware offers lightweight yet long-term use durability when compared with cast iron or stainless steel counterparts.
- Cost-Effective Production: Aluminium’s malleability facilitates cost-efficient deep drawing and stamping processes that result in efficient cookware shapes with minimum waste.
Anodized Aluminium Circle for Lighting
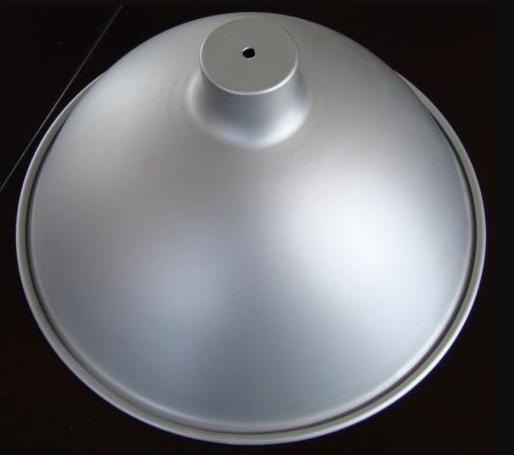
Anodized aluminium circles play an essential part in lighting fixtures, particularly LED lamps, reflectors, and lamp housings.
- Reflectivity: High-purity aluminium alloys such as 1050 or 1060 provide superior light reflectivity, making it the ideal material for LED reflectors and streetlights.
- Heat Dissipation: LED lights generate heat, and aluminium’s thermal conductivity allows it to dissipate efficiently – thus prolonging the lifecycle of lighting systems.
- Anodized Finishes: Anodizing increases corrosion resistance while creating colorful finishes on aluminium circles for both functional and aesthetic use.
- Lightweight and Rustproof: Aluminium doesn’t corrode, making it perfect for humid environments such as outdoor settings.
PVDF-coated or Painted Aluminium Circle for Decorative Items
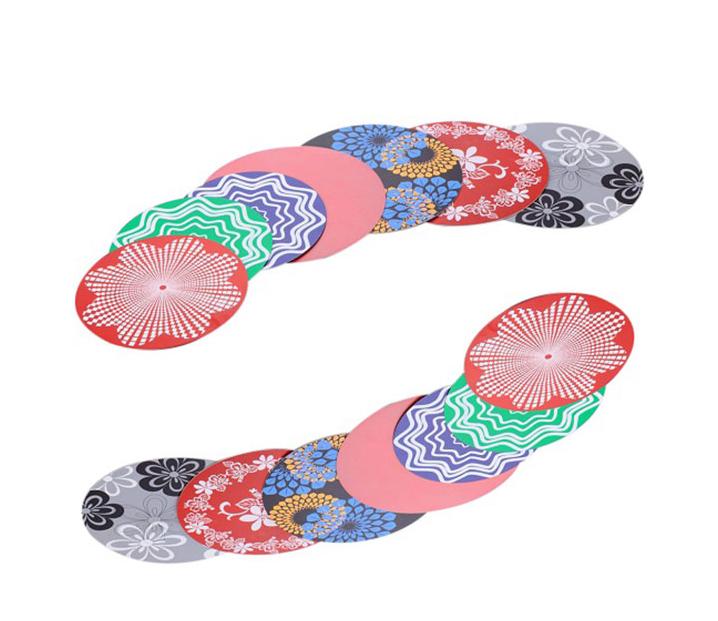
Aluminium circles have long been utilized as decorative items, signage and architectural components due to their adaptability in surface treatments.
- PVDF Coating: PVDF coating is an impact resistant fluoropolymer coating which offers weather and UV protection while boasting vibrant colors for outdoor signage and wall cladding applications.
- Painted Finishes: Powder-coated or spray-painted aluminium circles can be found used for home decor, nameplates and artistic installations.
- Custom Shapes & Designs: Aluminum allows designers to craft intricate custom shapes and designs by laser-cutting, embossing or etching intricate patterns for decorative panels or luxury interiors.
- Longevity: Aluminium offers superior longevity when compared with wood or plastic products, never warping, rotting, or discoloring over time, making it the material of choice for high-end decorative applications.
What are the Common Alloys of aluminium circle sheet
Aluminium circle sheets come in many alloy varieties to meet different industrial demands, offering properties tailored specifically for various industrial purposes. Your selection may depend upon factors like strength, formability, corrosion resistance and thermal conductivity – here are the most widely-used alloys:
- 1050 and 1060 (Pure Aluminium Series)
These alloys contain over 97% aluminium, making them highly corrosion resistant and thermal conductive, but soft enough for easily formed applications like cookware, chemical containers and reflectors.
- 3003 (Manganese-Alloyed Series)
With manganese added for enhanced strength, 3003 provides superior workability than pure aluminium while maintaining good corrosion resistance, making it widely used for lighting fixtures, kitchenware and general fabrication projects.
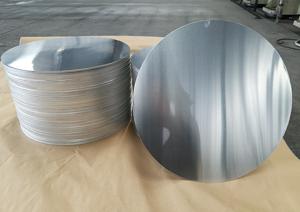
- 5052 (Magnesium Alloyed Series)
5052 is widely recognized for its exceptional strength and weldability, making it suitable for marine, automotive and industrial use. Furthermore, saltwater corrosion resistance makes 5052 an attractive material choice when building ships or fuel tanks.
- 6061 (Magnesium-Silicon Alloy)
This heat treatable alloy offers superior strength and machinability, making it popularly utilized in aerospace components, structural parts and high stress mechanical applications.
- 8011 (Al-Fe-Si Alloy)
8011 is commonly utilized as bottle caps and closures due to its excellent formability and sealing capabilities, often making for reliable food packaging solutions.
Each alloy is selected based on application needs, to guarantee optimal performance in industries spanning cookware to aerospace. Manufacturers frequently opt between these alloys when selecting those which best balance cost, durability and functionality requirements.
Conclusion
Aluminium circle sheets are essential in industries ranging from cookware to aerospace due to their lightweight, durability, and versatility. The manufacturing process ensures high precision, while different alloys and surface treatments allow customization for specific needs. Whether for non-stick pans, anodized lighting, or decorative panels, aluminium circles continue to be a preferred material for manufacturers worldwide.
Would you like additional details on any specific application or alloy? Contact Lanren, we are looking forward to providing you with the best products and service!
Related Products