What You Should Know Before Buying Aluminum Circle?
Aluminum circles are widely used in various industries for their versatility, durability, and lightweight properties. Whether you’re a manufacturer, product designer, or supplier looking to incorporate aluminum circles into your project, there are several key factors to consider before purchasing. Understanding the manufacturing process, types of aluminum circles, and your specific needs will help ensure you choose the right product. This guide can help you make an informed decision when purchasing aluminum circles.
Understand the Aluminum Circle Manufacturing Process
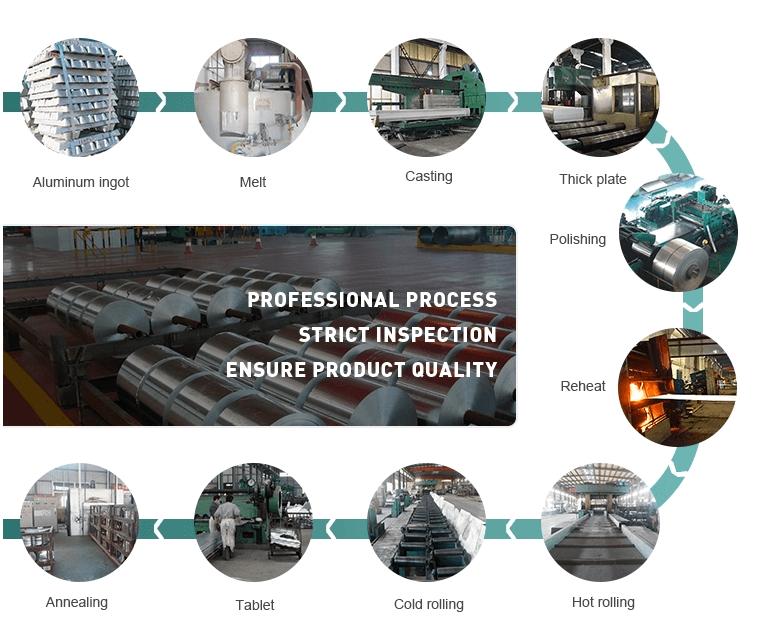
The production of aluminum circles involves several steps that ensure the final product meets specific quality and performance standards. The process typically includes the following stages:
- Casting: The process begins with raw aluminum metal cast into large ingots or slabs. These ingots serve as the primary material for creating aluminum circles. The quality of the ingot is essential, as it directly impacts the final properties and performance of the aluminum circle.
- Rolling: After the ingots are prepared, they are passed through a rolling mill, where the aluminum is gradually reduced in thickness. This process ensures the aluminum maintains its structural integrity while being transformed into thin sheets, or coils, which are then cut into aluminum circles.
- Blanking: After the aluminum has been rolled into thin sheets, the next step is blanking. In this phase, a press machine uses a die to cut out precise circular shapes from the aluminum sheet. These circles can vary in size and thickness, depending on the requirements of the end application.
- Heat Treatment: Certain aluminum circles undergo heat treatment to improve their mechanical properties, like strength and hardness. This process involves heating the aluminum to a precise temperature and then cooling it in a controlled environment to achieve the desired characteristics.
- Surface Treatment: Depending on their intended application, aluminum circles may undergo various surface treatments, including anodizing, polishing, or coating. These treatments enhance the material’s corrosion resistance, appearance, and overall durability.
By understanding the aluminum circle manufacturing process, you can gain insights into the material’s quality and performance characteristics. This knowledge will help you choose the right aluminum circles for your project while ensuring that the final product meets your specific needs.
Know the Types of Aluminum Circle
Aluminum circles come in various types, each designed to meet specific application requirements. The most common types are distinguished by the alloy used, the intended purpose, and the manufacturing process. Here are the main types of aluminum circles you should be aware of:
- Deep Drawing Aluminum Circles: These circles are crafted from high-purity, soft aluminum alloys, such as 1050 or 1060. Designed for deep drawing processes, they can be stretched or pressed into deeper shapes without cracking. Thanks to their excellent formability and ability to distribute heat evenly, these circles are commonly used in cookware production, including frying pans, woks, and other kitchen items.
- Spinning Aluminum Circles: In the spinning process, the aluminum circle is rotated at high speeds and shaped into a hollow, circular form, allowing for the creation of intricate designs. Typically made from alloys like 3003, which are soft enough to be shaped yet durable, these circles are used in applications such as aluminum containers, lamp covers, and decorative pieces.
- Cookware Aluminum Circles: These are specialized circles crafted for manufacturing kitchen products. They are often thicker and made from high-quality aluminum alloys like 3003, offering superior strength and thermal conductivity. These circles are essential for the production of pots, pans, and other cookware items that require excellent heat retention and resistance to corrosion.
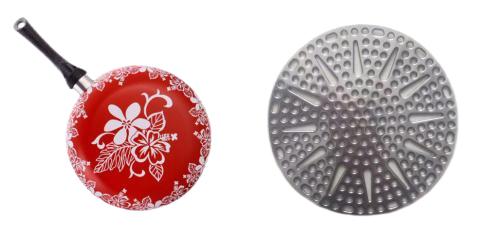
- Decorative Aluminum Circles: Used primarily in design and aesthetic applications, decorative aluminum circles often feature a smooth, polished finish or a matte surface for visual appeal. These circles are typically used in signage, interior decorations, and architectural elements where the appearance of the material is just as important as its functionality.
Each type of aluminum circle has its own unique properties and advantages, depending on the intended application. Understanding the differences will help you select the most suitable product for your needs.
Determine Your Need Aluminum Circle
Before purchasing aluminum circles, it’s crucial to clearly define your specific requirements to ensure you select the right product. Consider the following factors:
Alloy and Grade
Aluminum circles come in a variety of alloys, each offering different levels of strength, corrosion resistance, and formability. Common alloys include:
- 1050 and 1060: These are high-purity aluminum alloys known for their excellent workability and corrosion resistance, ideal for lightweight applications like cookware, electronics, and reflectors.
- 3003: A versatile alloy with good strength and corrosion resistance, commonly used in industrial applications, including traffic signs, roofing, and heating.
- 5052 and 5005: These are stronger alloys that offer enhanced corrosion resistance, particularly in marine environments, making them suitable for applications such as boat hulls, outdoor structures, and solar panels.
Choosing the right alloy ensures your aluminum circle meets the performance, strength, and durability requirements of your project.
Thickness and Size
The thickness and diameter of the aluminum circle depend on how it will be used. For instance:
- Thinner Circles: For applications like decorative purposes or signage, thinner circles (around 0.2–1 mm) may be sufficient.
- Thicker Circles: In applications like cookware, automotive parts, or industrial components, thicker circles (up to 6 mm or more) may be necessary to ensure durability and performance.
Make sure to select the thickness and size that align with both your functionality needs and budget constraints. Too thick or too thin can affect both performance and cost-effectiveness.
Surface Finish
The surface finish of the aluminum circle influences both its appearance and performance. Common finishes include:
- Polished finish: For applications requiring a shiny, smooth surface, such as cookware or decorative products.
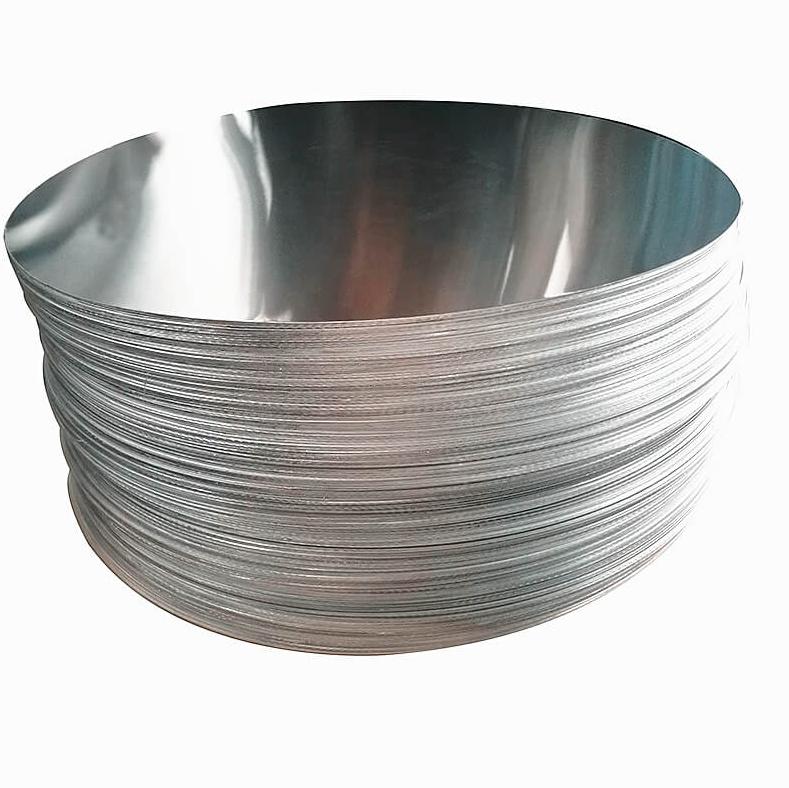
- Matte finish: Often used in industrial or signage applications, where a non-reflective, muted look is preferred.
- Anodized finish: For added durability and corrosion resistance, anodizing provides a protective layer, making it suitable for outdoor or marine applications.
When determining the surface finish, consider the environmental conditions the aluminum circle will be exposed to and whether any aesthetic qualities are needed for your product.
Select A Reliable Aluminum Circle Manufacturer
Choosing the right manufacturer for aluminum circles is crucial to ensuring high-quality products that meet your project specifications. When selecting a supplier, consider the following factors:
- Reputation: A manufacturer with a solid reputation in the industry is more likely to deliver products that meet your expectations. Look for customer reviews, certifications, and their history of providing reliable products.
- Quality Control: High-quality aluminum circles require rigorous quality control processes. Ensure the manufacturer has robust procedures for testing and inspecting products to guarantee consistency and compliance with your requirements.
- Customization: Depending on your project’s needs, you may require specific sizes, alloys, or surface finishes. A flexible manufacturer that can accommodate custom orders ensures your exact needs are met, saving time and money.
- Pricing: While it’s important to stay within budget, ensure that low pricing doesn’t come at the cost of quality. Compare quotes from multiple manufacturers to find the best balance between cost and quality.
- Delivery and Lead Time: Timely delivery is crucial, especially for large projects. Choose a manufacturer that can meet your deadlines and offers reliable shipping options.
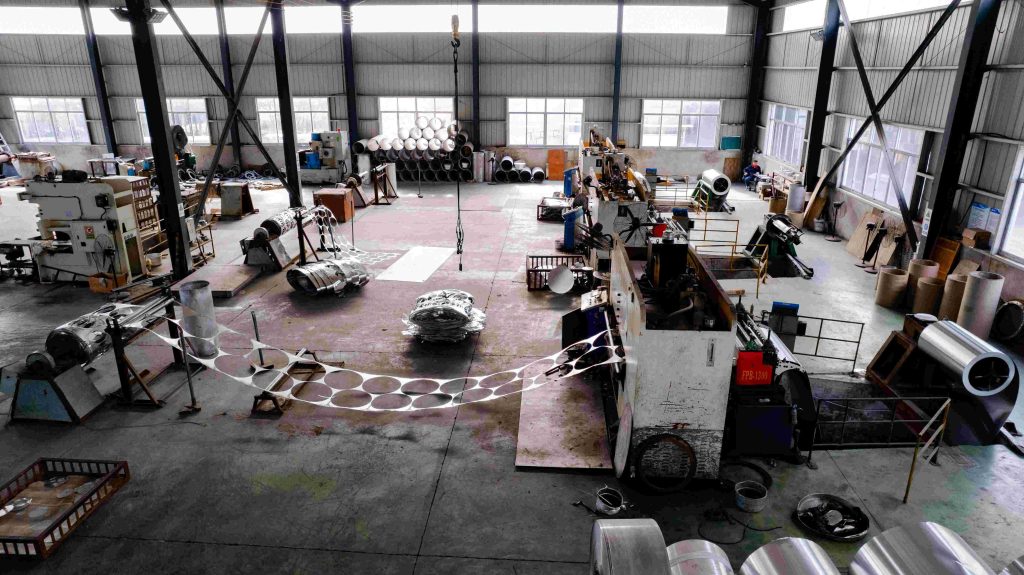
Lanren is a leading manufacturer of high-quality aluminum circles. With years of industry experience, Lanren offers a wide range of aluminum circles suitable for various applications, including cookware, automotive parts, and packaging. The company is committed to stringent quality control, ensuring that each aluminum circle meets the highest standards. With customized solutions and competitive pricing, Lanren stands out as a reliable partner for your aluminum circle needs, delivering consistent quality on time, every time.
For any aluminum circle needs, please feel free to contact us.