What are the Application of Induction Aluminium Circles?
Because of their unique features and manufacturing procedures, induction aluminum circles are useful and widely utilized in a variety of sectors. These round aluminum discs are specifically engineered for applications requiring good thermal conductivity, corrosion resistance, and lightweight properties.
What are Induction Aluminium Circles
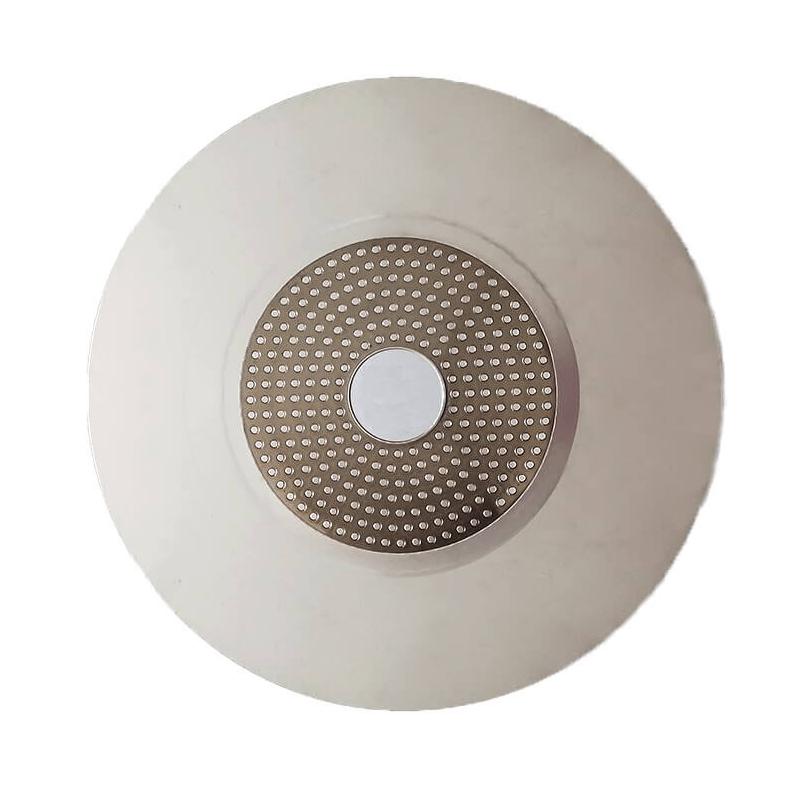
Induction aluminum circles are flat, round discs crafted from high-quality aluminum alloys, specifically designed for applications requiring excellent thermal conductivity, lightweight properties, and corrosion resistance. These circles are produced using a specialized induction heating process, which ensures uniformity in thickness, strength, and surface finish. The induction heating technique not only enhances the mechanical properties of the aluminum but also makes it suitable for high-temperature applications, such as cookware used on induction stovetops.
Aluminum circles are available in various diameters and thicknesses, typically ranging from 0.3mm to 10mm, and are made from alloys like 1050, 1060, 3003, and 5052, depending on the intended use. Their versatility and durability make them a popular choice across industries, including cookware, lighting, electronics, automotive, and packaging. Additionally, their recyclability and eco-friendliness align with modern sustainability goals. Induction aluminum circles are not only functional but also cost-effective, offering a perfect balance of performance and affordability for manufacturers and end-users alike.
How Induction Aluminium Circles are Made
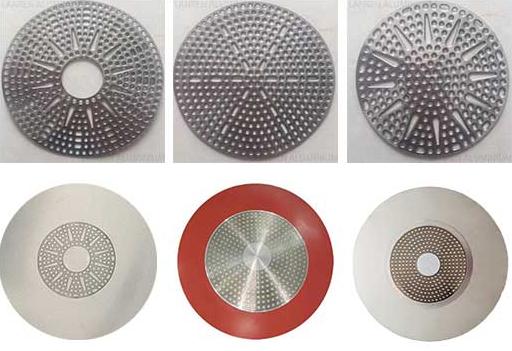
The manufacturing of induction aluminum circles is a rigorous procedure that combines advanced technology and precision engineering to produce high-quality, long-lasting discs. It starts with the selection of high-grade aluminum alloys like 1050, 1060, 3003, or 5052, which are chosen depending on the unique needs of the intended application. These alloys are melted in a furnace at high temperatures before being cast into massive billets or slabs. The billets are then heated and fed through a series of hot rolling mills, reducing their thickness and forming aluminum sheets. This hot rolling technique not only thins the material but also strengthens its structure.
Once the desired thickness is achieved, the sheets undergo cold rolling to refine their surface finish and enhance dimensional accuracy. Cold rolling also increases the strength and hardness of the aluminum. The sheets are then cut into circular shapes using precision cutting tools. The key step in the process is induction heating, where the aluminum circles are subjected to controlled electromagnetic induction. This treatment improves their mechanical properties, such as strength and uniformity, making them suitable for high-temperature applications like cookware.
Finally, the circles are cut, polished, and coated (if needed) to suit industry requirements. The end result is a high-performance product with good thermal conductivity, corrosion resistance, and durability, suitable for application in a variety of industries.
Key Applications of Induction Aluminium Circles
Induction aluminium circles are highly versatile and play a critical role in several industries due to their unique combination of lightweight, durability, and excellent thermal and electrical conductivity. Below are the four most important applications of induction aluminum circles, explained in detail:
Cookware Manufacturing
Induction aluminum circles are widely utilized in the manufacture of cookware, including as pots, pans, and frying pans. Their excellent thermal conductivity allows equal heat dispersion, which is critical for effective cooking. These circles are specifically intended to function on induction cooktops since the induction heating process improves their magnetic qualities, making them suitable for induction burners. Furthermore, aluminum’s lightweight nature makes cookware easy to handle, while its corrosion resistance maintains its lifetime even after repeated use. Many manufacturers attach non-stick coatings on these circles, which improves their functionality and appearance in modern kitchens.
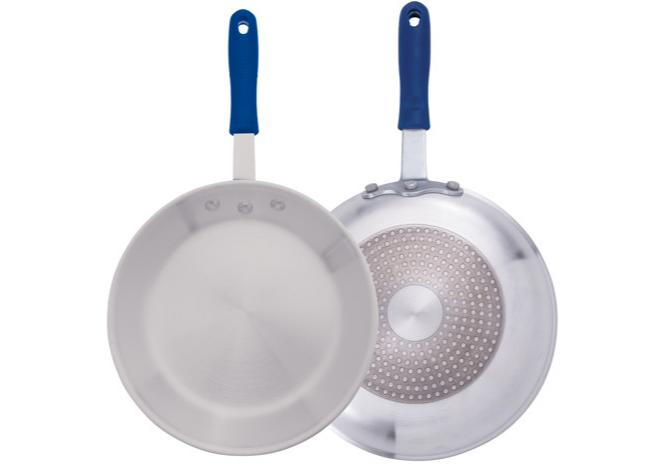
Electronics and Electrical Appliances
Induction aluminum circles are a key component in the electronics industry, particularly in the production of heat sinks, capacitors, and other electrical components. Their excellent thermal conductivity allows them to efficiently dissipate heat generated by electronic devices, preventing overheating and ensuring optimal performance. Aluminum’s electrical conductivity also makes it suitable for use in electrical appliances, where it helps maintain consistent performance and reliability. The lightweight nature of these circles is an added advantage, especially in portable devices where reducing weight is a priority. Additionally, the corrosion resistance of aluminum ensures that these components remain functional even in challenging environments.
Lighting Industry
In the lighting industry, induction aluminum circles are widely used to manufacture reflectors and lampshades for LED lights, streetlights, and automotive lighting systems. Aluminum’s natural reflectivity makes it an ideal material for directing and maximizing light output. The circles are often polished or coated to achieve a mirror-like finish, which improves light reflection efficiency. Furthermore, aluminum’s lightweight and corrosion-resistant properties make it suitable for outdoor and industrial lighting applications, where durability and performance are critical. The use of induction aluminum circles in lighting also contributes to energy efficiency, as they help reduce the weight of fixtures and improve heat dissipation.
Automotive Industry
The automotive industry relies heavily on induction aluminum circles for manufacturing various components, including wheel covers, trim pieces, and heat exchangers. Aluminum’s lightweight properties contribute to fuel efficiency by reducing the overall weight of vehicles, which is a critical factor in modern automotive design. The corrosion resistance of aluminum ensures that these components can withstand harsh environmental conditions, such as exposure to road salt and moisture. Induction aluminum circles are also used in the production of heat exchangers, where their thermal conductivity helps regulate engine temperature and improve vehicle performance. Their durability and ability to be easily molded into complex shapes make them a preferred choice for automotive applications.
These four applications highlight the versatility and importance of induction aluminum circles across industries. Their unique properties, combined with the precision of the induction heating process, make them indispensable in modern manufacturing and technology.
Benefits of Using Induction Aluminium Circles
Induction aluminum circles are highly prized for their distinct features, which are amplified by the induction heating process used in their production. This particular approach offers exceptional performance and allows for a wide range of applications. Here are the main advantages of employing induction aluminum circles, with a focus on their induction-specific features:
1. Superior heat distribution
The induction heating technique ensures that aluminum circles are heated evenly, resulting in consistent material properties. This makes them ideal for applications requiring precise and even heat distribution, such as induction cookware. The circles respond quickly to induction heating, resulting in efficient and controlled cooking experiences.
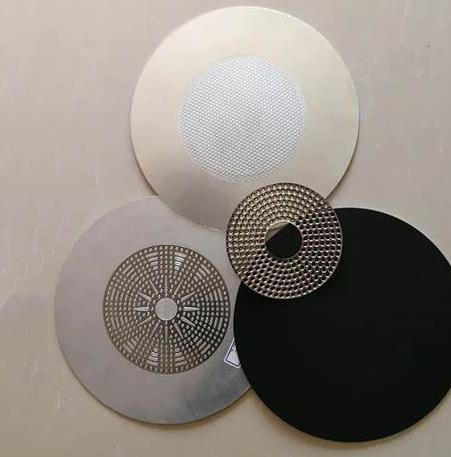
2. Enhanced Mechanical Properties
Induction heating improves the mechanical strength and durability of aluminum circles. The process eliminates internal stresses and enhances the material’s structural integrity, making it more resistant to deformation under high temperatures or mechanical loads.
3. Energy efficiency
Induction aluminum circles are designed specifically to work with induction cooktops, which are known for their energy efficiency. The rings heat quickly and direct heat to the cooking surface, reducing energy loss and cooking time.
4. Compatible with Induction Technology
Induction aluminum circles, as opposed to regular aluminum circles, are intended for use with induction cooktops. They contain ferromagnetic elements or are coated in induction-friendly materials, allowing them to interact with magnetic fields and produce heat.
Induction aluminum circles provide unrivaled performance, efficiency, and versatility by capitalizing on the unique benefits of the induction heating process, making them a popular choice for both industrial and consumer applications.
FAQs
- How do induction aluminum circles differ from regular aluminum circles?
Induction aluminum circles undergo a specialized induction heating process that enhances their mechanical properties, making them better suited for high-temperature applications like cookware. Regular aluminum circles may not receive this treatment, limiting their performance in demanding environments.
- What thicknesses are available for induction aluminum circles?
Induction aluminum circles are available in a variety of thicknesses, ranging from 0.3mm to 10mm. The thickness used is determined by the application’s specific performance requirements.
- Can induction aluminum circles be used with gas stoves?
Yes, induction aluminum circles can be used with gas burners. However, because of their magnetic qualities, they are specifically suited for induction cooktops and may function efficiently with induction heating technology.
- Are induction aluminum circles safe for food-related applications?
Absolutely. Induction aluminum circles are made from food-grade aluminum alloys, ensuring they are safe for food contact. They are often coated with non-toxic materials to further enhance their suitability for cookware and packaging.
- What are the thickness possibilities for induction aluminum circles?
Induction aluminum circles are available in a variety of thicknesses, ranging from 0.3mm to 10mm. The thickness used is determined by the application’s specific performance requirements.
- Can the induction aluminum circles be customized?
Yes, in Lanren Aluminium, induction aluminum circles can be customized to fit unique needs. Diameter, thickness, surface finish, and coatings are all customizable options that ensure they meet the specific needs of your project or business.
Related Products