Surface Treatments and Coatings for Aluminum Circles
Aluminum circles are widely used in various industries, from cookware to automotive applications, due to their light weight, durability and good thermal conductivity. When used, in order to improve their performance and life, aluminum discs usually need to be properly treated and coated. This article explores the surface characteristics of aluminum discs, the available treatment and coating options, and guidance on how to choose the right solution for your needs.
Overview of Aluminum Surface Properties
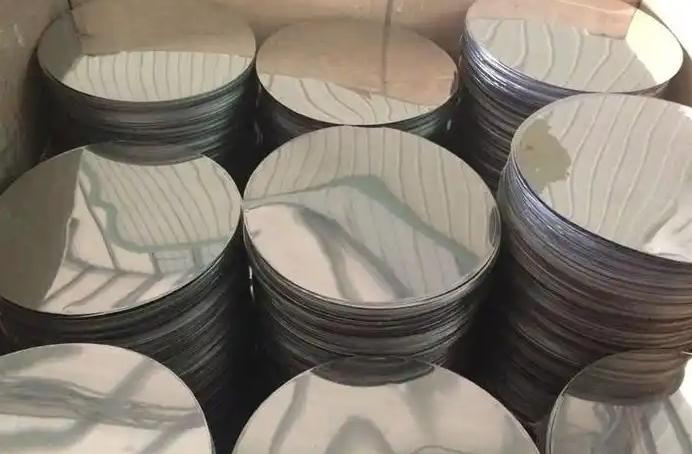
Aluminum is a versatile material widely used in various industries due to its excellent physical and chemical properties. However, understanding its surface characteristics is crucial for optimizing performance in specific applications. Key surface properties of aluminum include:
- Natural Corrosion Resistance: Aluminum forms a thin oxide layer when exposed to air, providing inherent protection against rust and corrosion.
- Lightweight and Durable: Its low density makes aluminum ideal for applications where weight reduction is critical, while its surface can be treated to enhance durability.
- Thermal and Electrical Conductivity: Aluminum efficiently conducts heat and electricity, making it suitable for cookware, electronics, and energy applications.
- Surface Softness: While easy to shape and form, untreated aluminum surfaces are prone to scratches and wear, requiring protective treatments.
- Aesthetic Versatility: Aluminum’s natural luster and reflectivity can be enhanced or altered through treatments, offering a wide range of decorative possibilities.
- Food Safety: With proper treatment, aluminum is non-toxic and safe for use in food-grade applications like cookware and packaging.
Despite these advantages, untreated aluminum surfaces can be vulnerable to environmental factors, wear, and damage. Proper surface treatments and coatings are essential to unlock its full potential and ensure long-term performance.
What are the Types of Surface Treatments for Aluminum Circles?
Surface treatments enhance the properties of aluminum circles, such as durability, corrosion resistance, and aesthetics. Below is a summary of the key surface treatments and their benefits:
Treatment Type | Description | Key Benefits | Common Applications |
Anodizing | Electrochemical process that thickens the natural oxide layer. | Corrosion resistance, wear resistance, and dyeability for coloring. | Cookware, decorative panels, electronics. |
Polishing | Creates a smooth, reflective surface using mechanical, chemical, or electrochemical methods. | Enhances aesthetics and reduces surface defects. | Decorative applications, reflectors. |
Etching | Chemical or mechanical process to create a matte surface or improve coating adhesion. | Reduces reflectivity and prepares surface for further coating. | Low-gloss finishes, industrial parts. |
Chemical Conversion Coatings | Involves chromate or phosphate treatments to enhance surface properties. | Improves corrosion resistance and serves as a primer for coatings. | Automotive, aerospace, general coatings. |
Brushing | Produces a uniform textured finish through abrasion. | Adds decorative texture and masks minor surface imperfections. | Home appliances, architectural panels. |
These treatments offer specific benefits depending on the intended application, ensuring that aluminum circles meet performance and aesthetic requirements effectively.
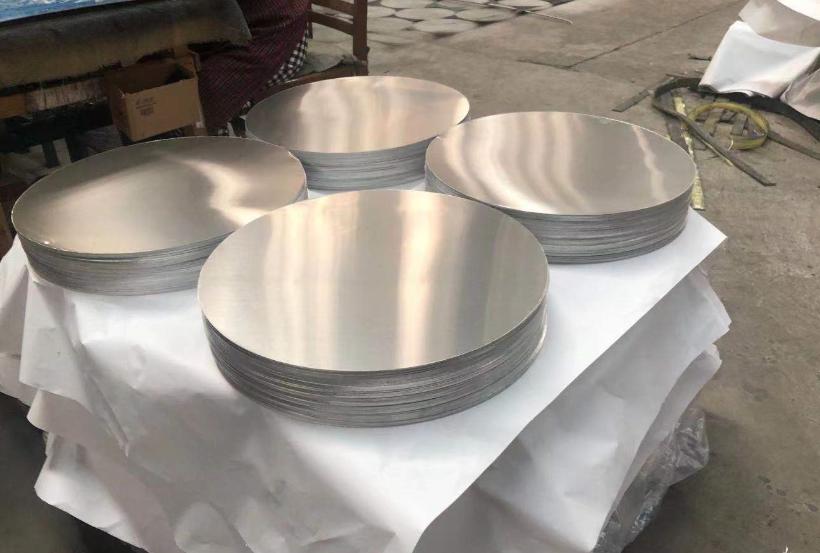
What are the Coating Options for Aluminum Circles?
Coatings enhance the performance and appearance of aluminum circles, offering protection against corrosion, wear, and environmental factors. The main coating options include:
Coating Type | Key Features | Common Applications |
Powder Coating | Durable, scratch-resistant, and environmentally friendly. Available in many colors and finishes. | Cookware, automotive, architectural. |
Paint Coatings | Offers aesthetic versatility with various finishes and functional properties like heat or weather resistance. | Decorative products, appliances, cookware. |
Anodized Coating | Thickens aluminum’s oxide layer for enhanced durability, corrosion resistance, and color options. | Decorative panels, industrial components. |
Non-stick Coatings | Provides a non-stick surface; includes PTFE and ceramic coatings. Heat-resistant and easy to clean. | Cookware, bakeware. |
Electroplating | Applies a metallic layer (e.g., nickel, chrome) for added wear resistance and aesthetic appeal. | Decorative items, luxury products. |
Anti-corrosion Coatings | Specialized coatings like fluoropolymer or epoxy to protect against harsh environmental conditions. | Marine, automotive, industrial applications. |
This concise format provides a clear comparison of each option’s features and applications, making it easy to understand their suitability for different purposes.
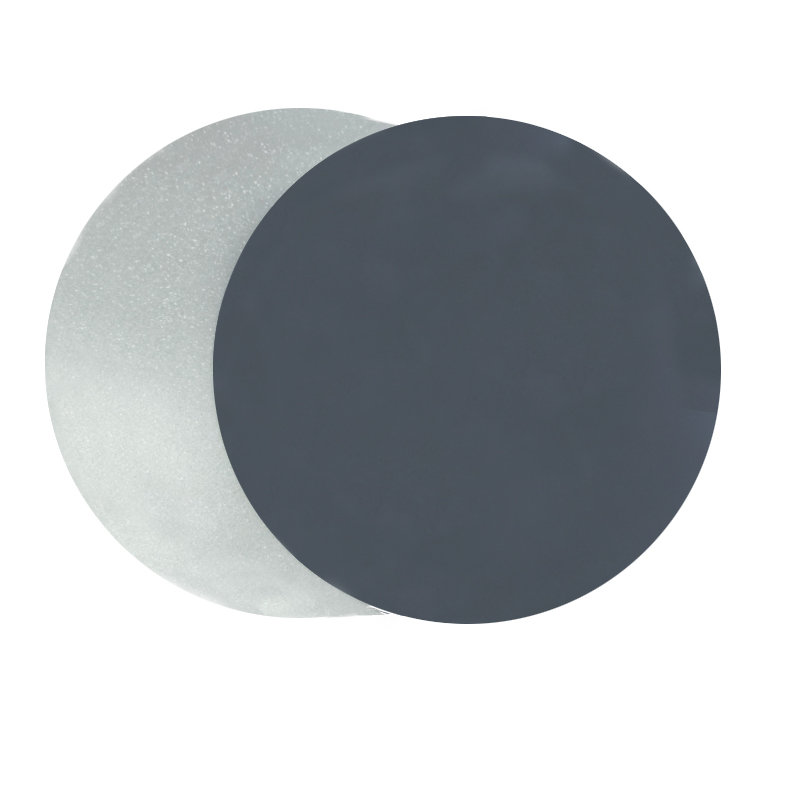
How to Choose Your Treatment or Coating for Aluminum Circles
Choosing the appropriate surface treatment or coating for aluminum circles is a critical decision based on specific application requirements and conditions. Below are the most important factors to consider when selecting the best treatment or coating for your aluminum circles:
Know Your Application Purpose
- Cookware & Food-Related Products: For applications in the kitchen, such as cookware, food storage, or food processing, the treatment or coating must be non-toxic and food-safe. Coatings like non-stick (PTFE or ceramic coatings) are often preferred for easy cleaning and resistance to high temperatures. These treatments ensure safety and performance in cooking environments.
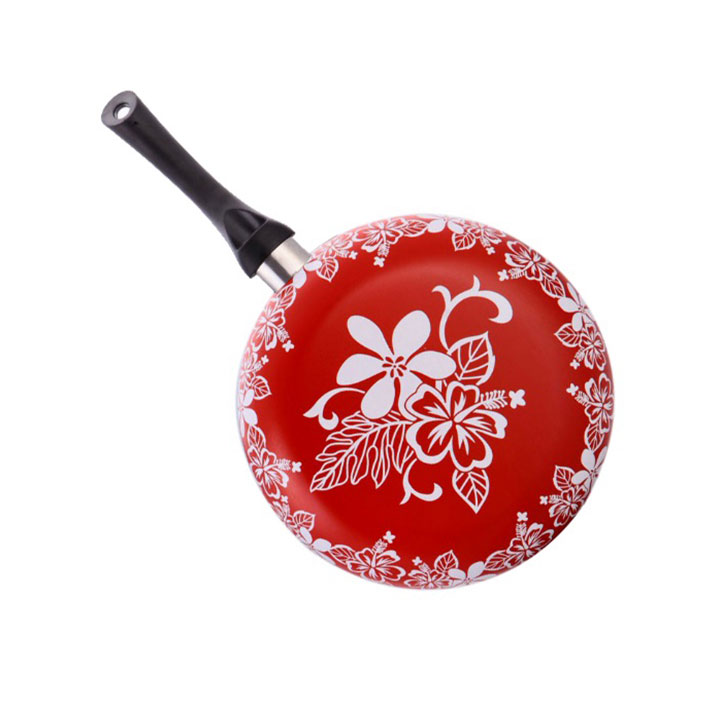
- Automotive & Aerospace: In the automotive and aerospace industries, aluminum circles require coatings that provide exceptional strength, corrosion resistance, and the ability to endure extreme temperatures. Powder coating and anodizing are ideal choices, offering durability, long-term protection, and a sleek, polished finish.
- Decorative & Architectural Uses: For decorative and architectural applications, such as panels, cladding, or lighting, aesthetic appeal is paramount. Anodizing enhances the visual appeal with a glossy, metallic finish, while powder coating offers a wide range of colors and textures. Brushed finishes are also favored for their elegant, matte appearance.
Consider the Environmental Exposure
- Corrosion Resistance: When aluminum circles are exposed to moisture, salty air, or chemicals, it’s crucial to select a treatment that enhances corrosion resistance. Anodizing forms a thick oxide layer that acts as a protective shield against rust, while chemical conversion coatings, such as chromate or phosphate, offer added protection in harsh environments.
- Heat Resistance: For aluminum circles used in high-temperature settings, such as industrial equipment, non-stick or ceramic coatings are ideal. These coatings are designed to withstand extreme heat without breaking down, making them perfect for cookware or high-performance machinery.
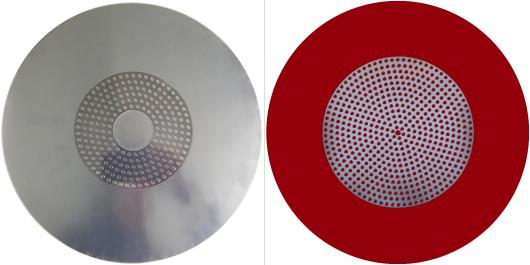
- UV and Weather Resistance: For aluminum exposed to outdoor elements, including UV rays and severe weather, powder coatings are often the optimal choice. These coatings are highly resistant to fading, chalking, and degradation caused by UV exposure, making them well-suited for exterior architectural applications.
By Your Aesthetic Requirements
- Shiny and Reflective Finishes: For applications that demand a highly reflective or glossy finish, anodizing is an excellent choice. This process not only enhances aluminum’s natural shine but also increases its durability, making the surface more resistant to scratches and oxidation. It is commonly used in consumer electronics and decorative products where visual appeal is crucial.
- Custom Colors and Textures: Powder coating provides a wide range of color and texture options, from matte to glossy finishes. Its versatility makes it ideal for products requiring specific brand colors or unique aesthetic designs, such as in the furniture or consumer goods industries.
- Subtle, Matte Finishes: For a more refined or brushed look, brushing or etching treatments can be applied. These techniques create a uniform texture, offering a more understated appearance that is ideal for architectural applications or decorative components that need to blend seamlessly with their environment.
Requirements for Durability and Wear Resistance
- High Abrasion Resistance: For aluminum circles exposed to heavy wear or abrasion, such as in automotive or industrial applications, coatings like electroplating (nickel or chrome) or powder coating provide an extra layer of protection. These coatings enhance the surface’s resistance to scratches, dents, and other mechanical stresses.
- Long-Term Durability: For applications requiring extended performance in demanding conditions, anodizing offers robust protection and increased durability. It resists chipping, peeling, and fading, making it ideal for products that need to withstand prolonged use.
- Easy Maintenance: Coatings like non-stick (for cookware) or powder coating not only offer durability but also facilitate easier cleaning and maintenance. These coatings resist staining, buildup, and contamination, making them essential for applications where cleanliness and hygiene are critical, such as in the food industry.
By considering these essential factors, you can make an informed decision when selecting the ideal surface treatment or coating for your aluminum circles.
Need to Find An Aluminum Circles Manufacturer?
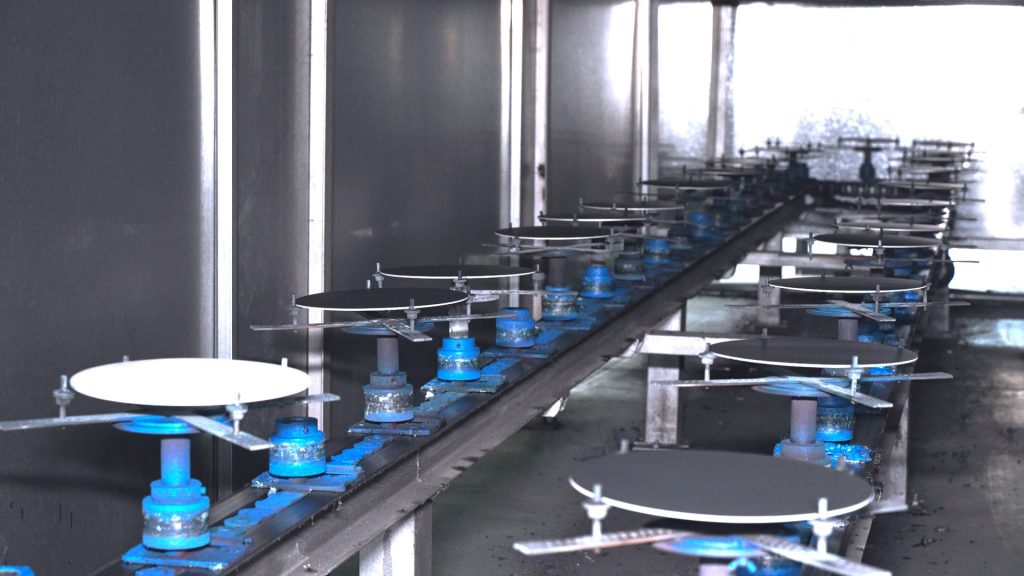
If you’re looking for a reliable aluminum circles manufacturer, Lanren Aluminium is an excellent choice. With over 15 years of experience, Lanren Aluminium is a leading supplier in the aluminum industry, specializing in high-quality aluminum products including circles, sheets, and cookware.
We offer a comprehensive range of products and services, ensuring consistent quality and customized solutions. Our advanced production facilities and skilled workforce allow them to meet diverse industry needs, from food-grade aluminum circles to high-performance applications.
For more information or inquiries, visit our website at Lanren Aluminium.