How to Choose the Right Grade of Aluminum Circle
Aluminum circles, often referred to as aluminum discs, are versatile materials widely used in a variety of industries. Their adaptability, lightweight nature, and corrosion resistance make them an ideal choice for applications ranging from cookware to industrial machinery. Choosing the right grade of aluminum circle can significantly impact the performance and longevity of your product. This guide will help you navigate the selection process effectively.
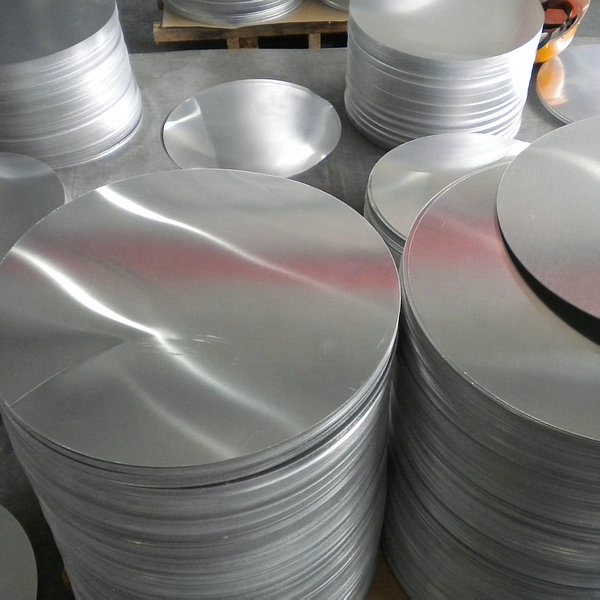
Common Applications of Aluminum Circle
Aluminum circles are incredibly versatile, finding applications across numerous industries due to their lightweight, durable, and corrosion-resistant properties. Below are some of the most common uses:
- Cookware Production: Aluminum circles are essential in the cookware industry due to their superior heat conductivity and corrosion resistance. These qualities make them ideal for crafting pots, pans, and kettles. Their ability to distribute heat evenly ensures consistent cooking performance, enhancing the reliability and efficiency of kitchen utensils.
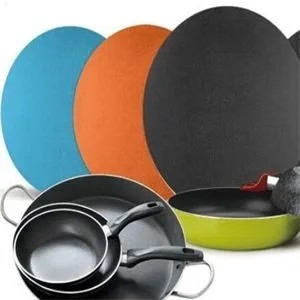
- Lighting Fixtures: Thanks to their high reflectivity and lightweight characteristics, aluminum circles are frequently used in the production of lighting reflectors and decorative covers. They contribute to energy-efficient designs and stylish appearances.
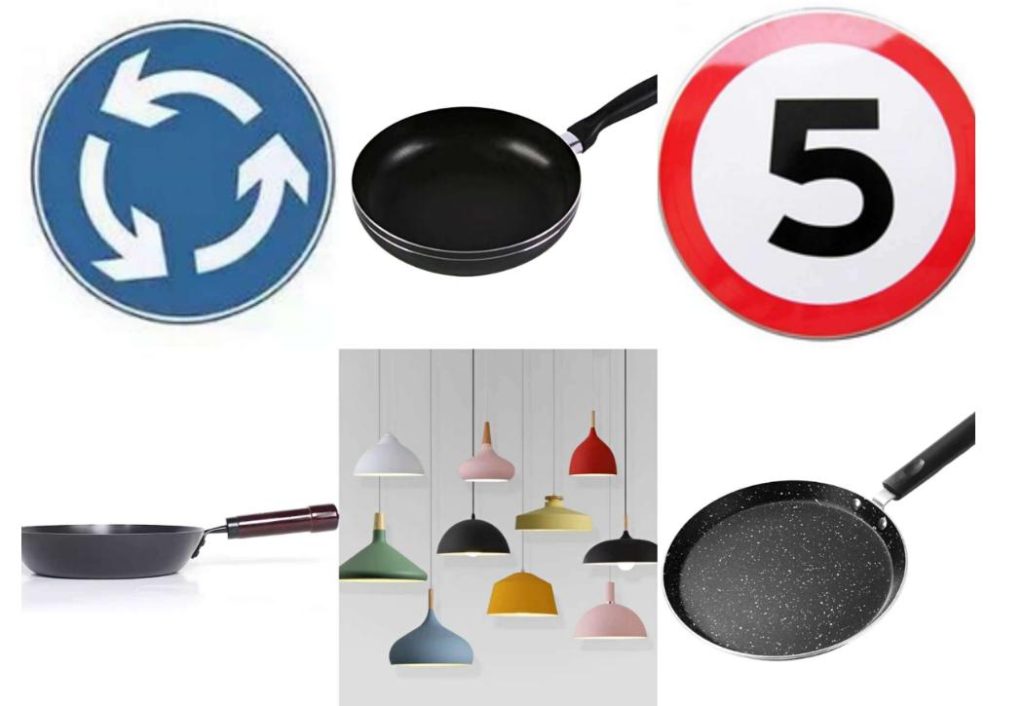
- Automotive Industry: Aluminum circles play a critical role in manufacturing lightweight yet durable automotive components, including wheel covers, fuel tanks, and decorative trims. Their high strength and corrosion resistance ensure reliable performance and longevity across diverse driving conditions.
- Electronics and Appliances: With exceptional thermal conductivity, aluminum circles are an ideal choice for heat sinks and electronic device components. They are also commonly used in small appliances, such as pressure cooker bases and other heat-sensitive parts.
- Industrial Equipment: Aluminum circles are employed in creating durable, lightweight parts for industrial machines and equipment. Their flexibility allows for easy fabrication, making them adaptable to diverse manufacturing needs.
These varied applications underscore the importance of selecting the right grade of aluminum circle for optimal performance.
Common Aluminum Grades for Aluminum Circles
Selecting the right aluminum grade is essential to match the specific requirements of your project. Below are some of the most commonly used grades for aluminum circles, along with their key characteristics:
- 1050: This grade is known for its exceptional corrosion resistance and outstanding formability. Its high ductility makes it easy to shape, making it an ideal choice for cookware, decorative applications, and electrical uses due to its excellent conductivity.
- 1100: A commercially pure aluminum grade, 1100 offers superb corrosion resistance and excellent workability. It’s commonly used for products requiring extensive forming and shaping, such as kitchen utensils, reflectors, and chemical equipment.
- 3003: Alloyed with manganese, this grade provides enhanced strength compared to 1050 and 1100 while maintaining good corrosion resistance. Its versatility makes it suitable for cookware, roofing, and light-duty industrial applications.
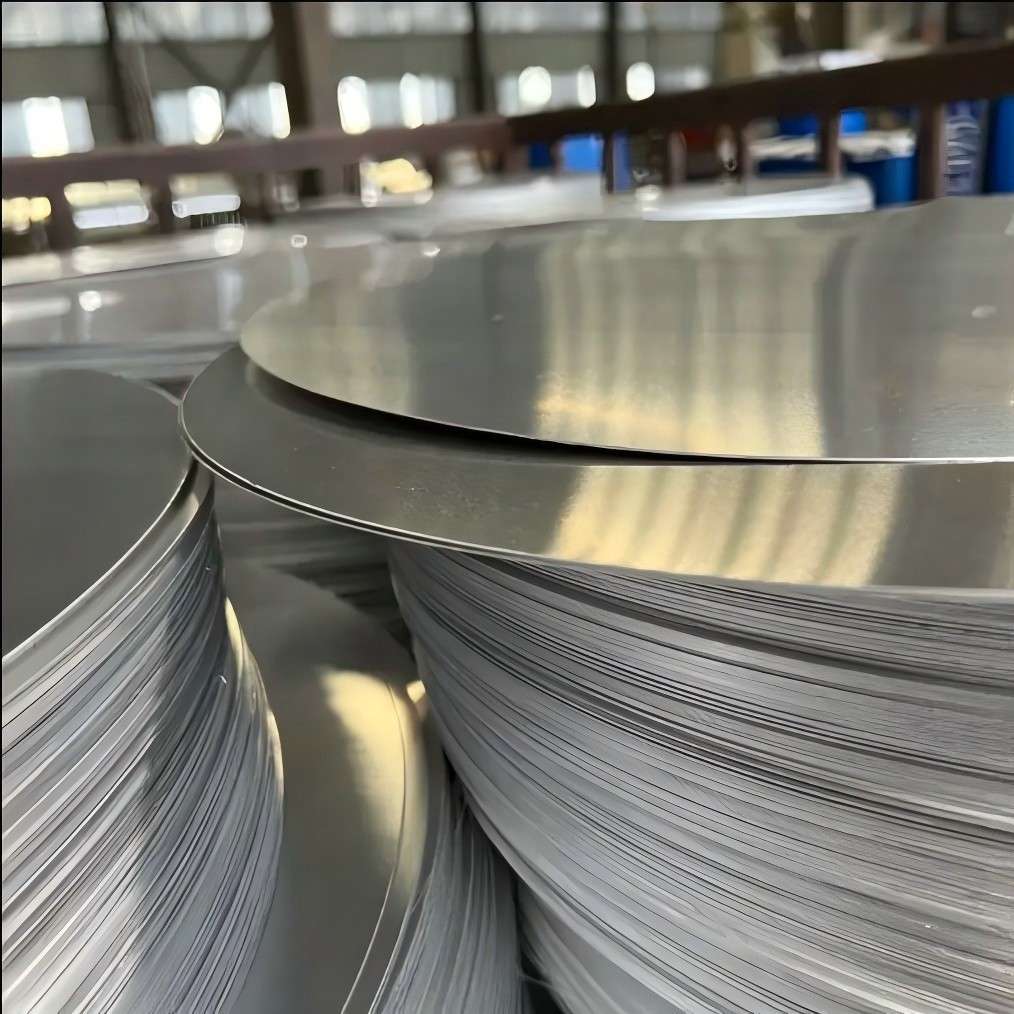
- 5052: Renowned for its exceptional corrosion resistance, especially in marine environments, 5052 aluminum is a high-strength alloy ideal for demanding applications such as boat construction, automotive parts, and equipment exposed to harsh conditions. Its durability and performance in saltwater and other corrosive environments make it a top choice for applications requiring long-lasting protection.
- 6061: Known for its outstanding starength and versatility, 6061 aluminum excels in both weldability and machinability, making it perfect for structural and heavy-duty applications. Commonly used in industries like aerospace, transportation, and construction, 6061 aluminum circles are durable, resistant to wear, and ideal for high-performance, long-lasting products.
Each grade of aluminum offers a distinct set of properties that makes it suitable for specific uses, so selecting the right grade depends on the requirements of the project at hand.
Factors to Consider When Choosing Aluminum Circle Grades
- Application Requirements
The most important consideration when selecting an aluminum circle grade is its intended use. Each grade offers distinct properties tailored to specific applications. For instance, grades like 1050 and 1100 are well-suited for cookware, where excellent thermal conductivity and corrosion resistance are critical. On the other hand, industries like automotive or marine demand stronger materials, making grades such as 5052 and 6061 a better fit due to their superior strength and durability. By understanding the specific needs of the application, you can select the optimal grade for maximum performance.
- Strength and Durability
Strength and durability requirements vary by application. For structural or high-stress uses, stronger grades like 6061 or 5052 are ideal. These grades offer superior tensile strength and are perfect for the automotive and aerospace industries. For applications requiring moderate strength, grades like 1050 and 1100 provide the necessary flexibility while maintaining durability.
- Corrosion Resistance
Corrosion resistance is vital for aluminum circles exposed to harsh environments. For applications in marine, outdoor, or industrial settings, grades with higher corrosion resistance, such as 5052, are preferred due to their ability to withstand saltwater and other corrosive elements. For general indoor use or in milder conditions, alloys like 1050 or 1100 offer adequate protection. The specific environmental conditions will dictate the appropriate grade to ensure long-term durability and prevent degradation.
- Formability and Workability
Formability is important when the aluminum circle needs to be shaped or cut. Grades such as 1050 and 1100 are known for their excellent workability and are suitable for intricate designs, like cookware. In contrast, stronger grades like 6061 are less malleable but can still be worked with advanced techniques. Choosing the right grade ensures ease of manufacturing and customization.
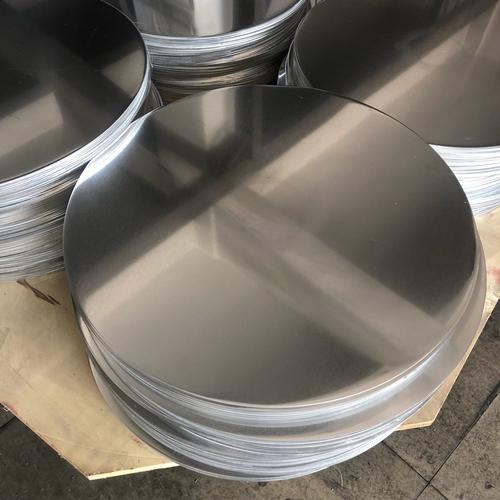
Tips for Working with Aluminum Circles
Here are some tips for you when working with aluminum circles:
- Cutting and Shaping: To ensure clean cuts and prevent damage when cutting or shaping aluminum circles, use sharp, specialized tools. CNC machines or laser cutters are ideal for achieving precise shapes. When bending aluminum, maintain a large bend radius to minimize the risk of cracking.
- Welding: Select the appropriate welding method, such as MIG or TIG, based on the specific aluminum grade (e.g., 6061 or 5052). Make sure the aluminum is clean and free of contaminants, and consider preheating the material to reduce the risk of cracking, particularly with higher-strength grades.
- Anodizing: For corrosion resistance and an attractive finish, select alloys like 5000 or 6000 for anodizing. Be mindful of the anodized layer’s thickness and quality to meet your project’s durability and aesthetic needs.
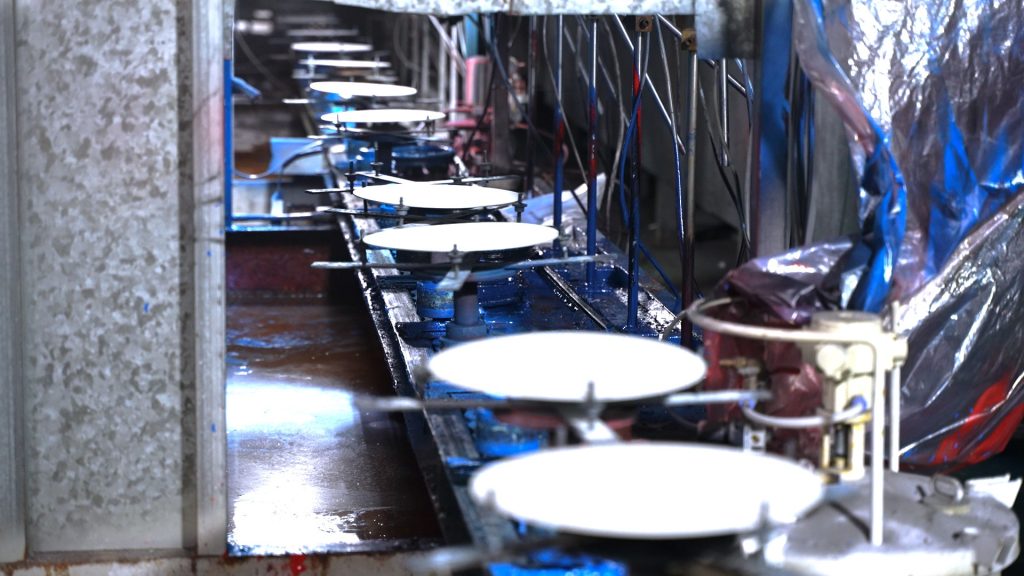
- Storage: Store aluminum circles in a dry, clean environment to avoid scratches and oxidation. Use protective covers or soft materials between layers to keep the aluminum in optimal condition.
- Recycling: Aluminum is highly recyclable, making it an eco-friendly choice. Collect scrap material during production to minimize waste, reduce costs, and contribute to environmental sustainability.
Summary
Choosing the right grade of aluminum circle is key to optimizing performance, efficiency, and durability. By considering application requirements, material properties, and cost, you can make an informed decision. Understanding common aluminum grades and following best practices will ensure the success of your project, delivering results tailored to your needs.
Related Products