How Aluminum Utensils Are Made?
Aluminum utensils are widely used in daily life, ranging from kitchen cookware such as pots and pans to specialized containers in industrial applications. Aluminum’s advantages, including its lightweight nature, excellent thermal conductivity, and certain degree of corrosion resistance, make it an ideal material for manufacturing utensils. The production of aluminum utensils involves a multi-step process, including careful selection of raw materials, the application of various manufacturing techniques, and final finishing and packaging. Through a series of complex and well-organized procedures, aluminum is ultimately transformed into a variety of practical and aesthetically pleasing utensils for everyday use.
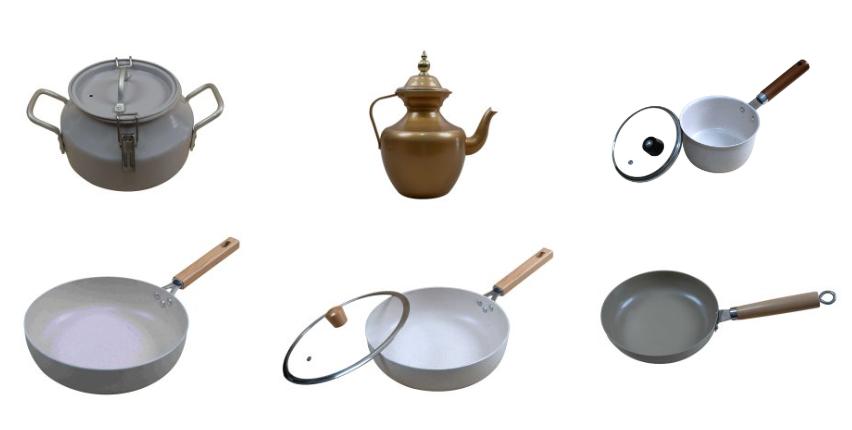
Raw Materials and Preparation
The manufacturing of aluminum utensils begins with selecting the right type of aluminum. Pure aluminum (99.5% or higher) is commonly used for its excellent thermal conductivity and lightweight properties. However, aluminum alloys, which combine aluminum with other metals like magnesium or silicon, are also popular for their enhanced strength and durability.
Aluminum alloys commonly used in utensil manufacturing include:
- 1100 Aluminum Alloy: Pure aluminum with 99% or higher aluminum content. With highly resistant to chemical reactions, making it safe for food contact.
- 3003 Aluminum Alloy: Contains manganese for enhanced corrosion resistance. The lightweight, strong, and highly formable, making it ideal for cookware and kitchen utensils.
- 5052 Aluminum Alloy: Known for its excellent resistance to corrosion, especially in marine environments. Their higher strength and durability, making it suitable for heavy-duty cookware.
These alloys are chosen based on their properties, such as strength, corrosion resistance, thermal conductivity, and ease of fabrication.
Aluminum is typically sourced as ingots or large sheets. In some cases, recycled aluminum is also used, contributing to environmental sustainability. Before manufacturing begins, the raw aluminum undergoes preliminary treatments such as cleaning and inspection to ensure quality. The aluminum is then melted and cast into slabs or billets, forming the foundation for the utensil-making process.

Aluminium Utensils Manufacturing Process
The production of aluminum utensils involves multiple stages, each carefully designed to transform raw aluminum into high-quality kitchen tools. These stages including:
Shaping the Aluminum: Casting and Forging
Casting
Casting is one of the most commonly used methods for shaping aluminum utensils. High-pressure die casting is particularly efficient, where molten aluminum alloy is injected into precision molds under high pressure. This technique is ideal for creating utensils with intricate patterns, such as decorative kitchenware. The molds, typically made from high-strength steel, consist of two parts that can be opened and closed. The molten aluminum alloy rapidly fills the mold cavity under high pressure and solidifies to form components that mirror the mold’s shape. For more flexible production, sand casting is used. In this process, a sand mold is created, and the aluminum alloy is poured into it. While sand casting is cost-effective and suitable for small-scale production, it often requires additional finishing to achieve the desired quality.
Forging
Forging involves applying pressure to aluminum or aluminum alloy billets to induce plastic deformation. In open-die forging, simple tools like hammers and anvils are used to shape billets into basic utensil components. This method is ideal for creating simple shapes with minimal precision requirements. Closed-die forging, on the other hand, uses custom molds to produce complex and precise components, such as ergonomic handles for high-end cookware. Forging compacts the internal structure of aluminum, enhancing its strength and durability.
Casting and forging provide essential methods for shaping aluminum utensils. Each technique offers unique advantages, allowing manufacturers to choose the most suitable method based on production needs and product requirements.
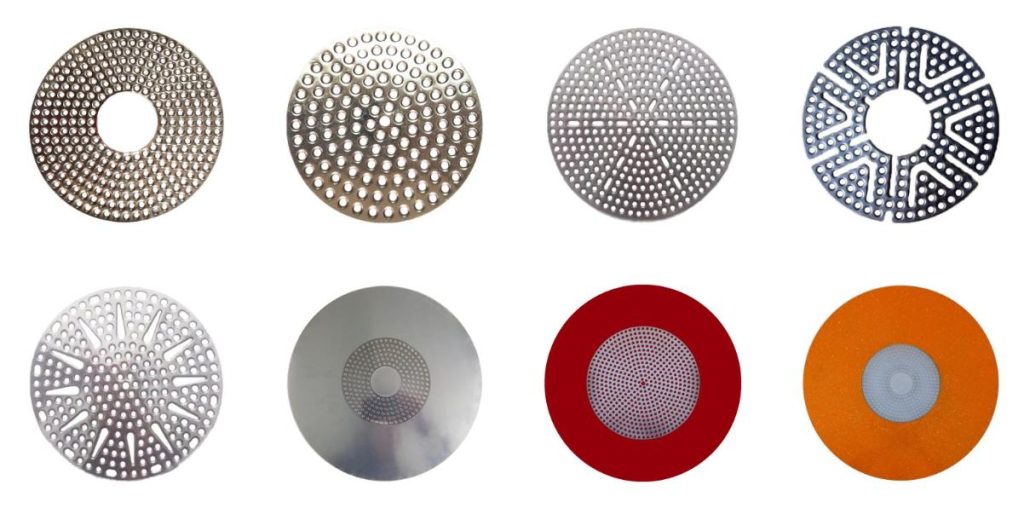
Adding Functionality: Anodizing and Coating
Anodizing
Anodizing is an electrochemical process that forms an oxide layer on the surface of aluminum utensils. The utensil acts as the anode and is submerged in an electrolyte solution, such as sulfuric acid, while a direct current is applied. During this process, aluminum atoms lose electrons and are oxidized, forming a dense layer of aluminum oxide. The thickness of the oxide layer can be controlled by adjusting the electrochemical conditions. Anodizing not only improves hardness and wear resistance but also significantly enhances corrosion resistance. Moreover, the porous nature of the anodized layer allows for dyeing, enabling utensils to be produced in a variety of colors, increasing their aesthetic appeal.
Coating
In addition to anodizing, coatings are often applied to aluminum utensils to enhance their functionality. For example, non-stick coatings, typically made from fluoropolymers, are applied to cookware. The coating process involves thorough surface preparation to ensure strong adhesion. These coatings provide desirable properties like non-stick performance and easy cleaning, greatly improving usability in kitchen environments.
Anodizing and coatings add value to aluminum utensils by improving functionality, durability, and aesthetics, meeting the needs of modern consumers.
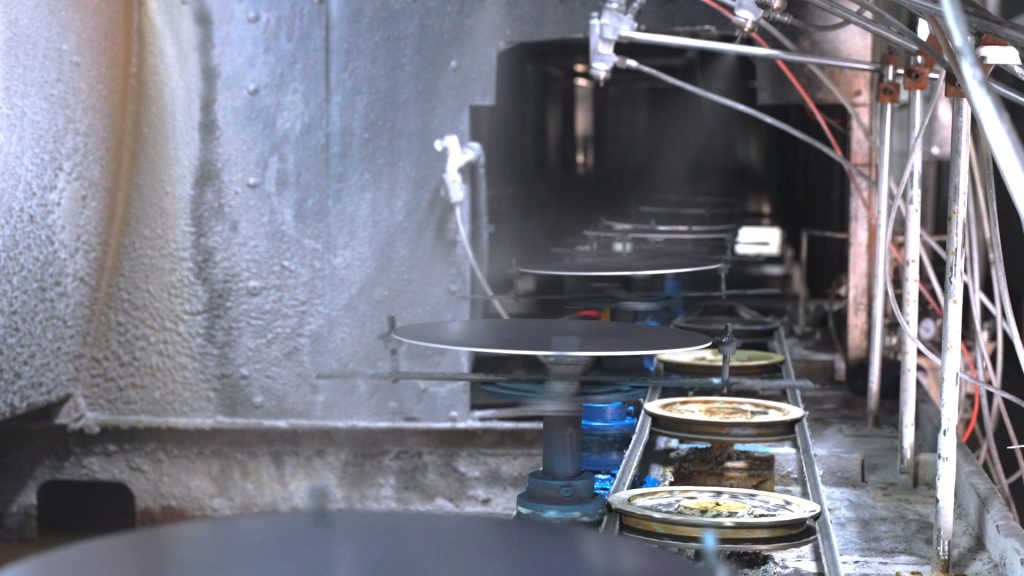
Finishing Touches: Polishing and Packaging
Polishing
Polishing enhances the surface quality and appearance of aluminum utensils. Mechanical polishing is a common method, using polishing wheels made from soft materials like cloth, combined with polishing compounds. As the wheel rotates at high speed, it smooths the utensil’s surface, removing minor imperfections and reducing surface roughness. For complex shapes, chemical polishing may be used, where aluminum reacts with a chemical solution to produce a smooth finish.
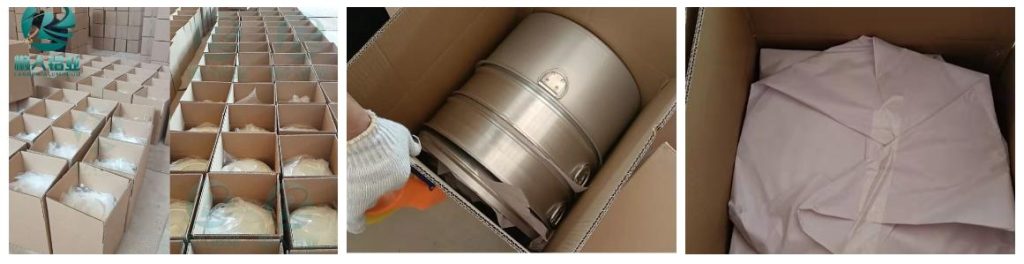
Packaging
Packaging is the final step in aluminum utensil manufacturing. Different utensils require tailored packaging solutions. Small utensils may be individually wrapped in plastic film and grouped together, while larger cookware often comes in cardboard boxes with foam inserts to prevent damage during transport. Packaging not only protects the utensils but also plays a vital role in marketing by appealing to consumers through attractive designs.
Polishing and packaging ensure that aluminum utensils are both visually appealing and well-protected, delivering a high-quality product to consumers.
The manufacturing process transforms raw aluminum into versatile utensils through a combination of precision techniques and rigorous quality checks. Each step ensures the final product meets both functional and aesthetic standards.
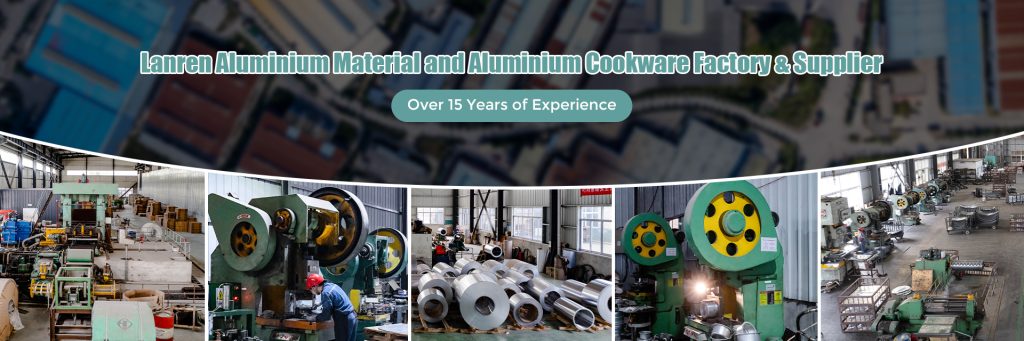
A Reliable Aluminum Utensils Manufacturer – Lanren
When it comes to high-quality aluminum utensils, Lanren stands out as a trusted manufacturer. With decades of expertise in aluminum processing, Lanren specializes in producing a wide range of cookware that meets international quality standards.
Commitment to Quality
We prioritize quality control of raw materials, sourcing premium aluminum and alloy materials from reliable suppliers. In terms of manufacturing processes, Lanren utilizes advanced casting and forging equipment and boasts extensive expertise in functional enhancement techniques such as anodizing and coating. For instance, our anodizing production line can precisely control the thickness and quality of the oxide layer, producing aluminum utensils with uniform coloration and excellent corrosion resistance. During the finishing stage, Lanren’s polishing process achieves an exceptionally high surface smoothness, while their packaging designs are both aesthetically pleasing and practical.
Wide Product Range
Lanren’s product lineup includes everything from basic kitchen utensils to specialized cookware. Their focus on innovation ensures that their products cater to the evolving needs of modern kitchens.
Aluminum utensil manufacturing is a blend of science, technology, and craftsmanship. From sourcing high-quality aluminum to ensuring flawless finishes, every step plays a vital role in delivering utensils that are reliable and long-lasting. With trusted manufacturers like Lanren, you can confidently invest in aluminum utensils that make cooking easier and more enjoyable.
Related Products