How Aluminium Circles Are Made?
Aluminum circles are versatile, lightweight, and durable and are used in a variety of industries, including cookware, automotive manufacturing, aerospace, and electronics. But have you ever wondered how these essential circles are made? This article will take you through the entire process from raw material to finished product, highlighting the importance of quality control, some of the top manufacturers in the industry today, and why investing in aluminium circles is a smart choice.

Raw Materials of Aluminium Circles
The production of high-quality aluminium circles begins with the selection of premium raw materials. The primary material used is aluminium alloy, which is chosen based on the specific properties required for the final application. The most commonly used aluminum alloy series for manufacturing circles include the 1000, 3000, and 5000 series, each offering unique characteristics:
- The 1000 Series consists of almost pure aluminum, with a purity of 99% or higher, making it extremely corrosion-resistant, lightweight, and easy to shape. This series is ideal for applications that require excellent workability and a smooth finish, such as cookware and decorative items.
- In the 3000 Series, alloys are primarily composed of manganese, which enhances both strength and durability without sacrificing formability. As a result, the 3000 series is commonly used in applications like signage, lighting, and various industrial components.
- The 5000 Series, on the other hand, features magnesium as the main alloying element, which offers superior strength, excellent weldability, and exceptional resistance to corrosion. Alloys from this series are typically used in demanding environments, including marine applications, transportation, and heavy machinery.
Raw aluminium is generally obtained as large billets, ingots, or coils. These are subsequently processed into thin sheets, which serve as the foundation for cutting and shaping aluminium circles. The selection of alloy and grade is based on the intended application of the circles, ensuring they possess the necessary mechanical, thermal, and chemical properties for the specific use. By using high-quality raw materials from the outset, manufacturers are able to produce aluminium circles that are durable, reliable, and customized to meet the demands of different industries.
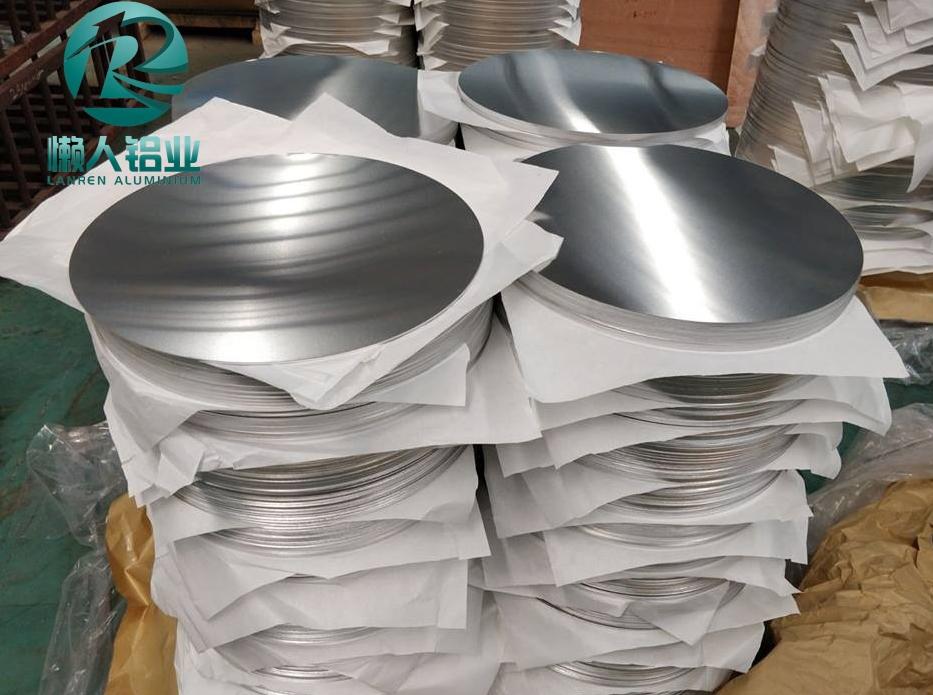
Aluminium Circles Making Process
Once the raw aluminum material is prepared, the next step involves shaping the aluminium into circles. This process requires precision to ensure each circle meets the exact specifications. Here’s how it works:
- Slitting: The initial step involves slitting the large aluminium coils into narrower strips, according to the required width for the circles. This process makes the material more manageable and simplifies further handling.
- Annealing: Often, the aluminium strips go through an annealing process. This heat treatment softens the metal, enhancing its malleability and relieving internal stress. As a result, the aluminium becomes easier to shape, and the risk of cracks or defects during punching is minimized.
- Cutting into Circles: Once the strips have been annealed, they are ready to be cut. Typically, a punching die or stamping machine is employed to shape the strips into uniform circles. The punching machine exerts high pressure to precisely punch out the circles. While the size of the circles can be customized to meet customer specifications, the primary objective is to ensure consistent quality and precise dimensions.
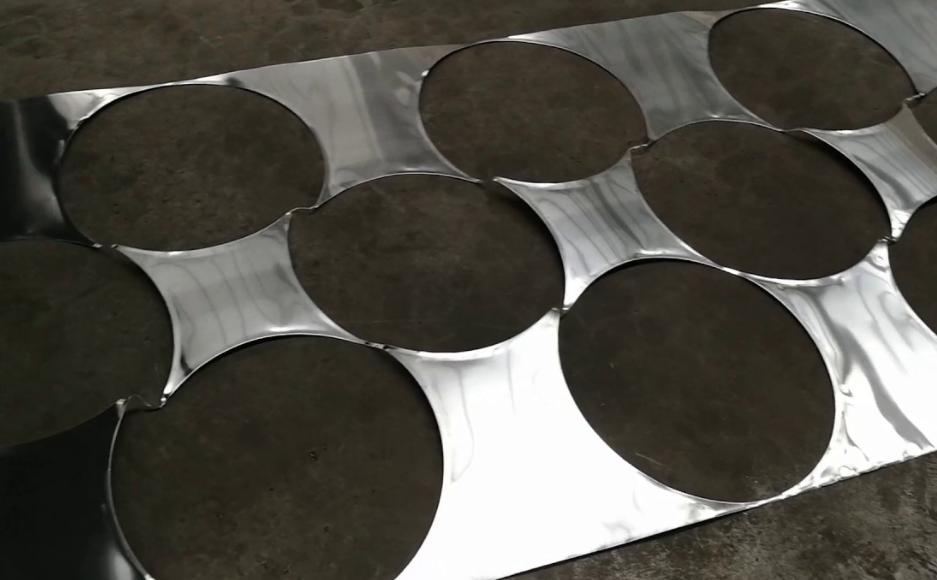
- Deburring: Following the punching process, the edges of the circles usually need to be smoothed. This process, known as deburring, involves eliminating any sharp or uneven edges left from cutting. Deburring can be achieved through mechanical methods, such as grinding, or by using a chemical treatment. The outcome is a smooth, clean-edged aluminium circle, ready for further processing or immediate use.
By following these steps, manufacturers ensure that the aluminium circles are precisely shaped and free of imperfections, making them suitable for a wide range of applications, from cookware to industrial components.
Aluminium Circles Quality Control and Inspection
Quality control in the aluminium circle manufacturing process is essential to ensure the final product meets both industry standards and customer requirements. Below is a summary of the key stages involved in inspecting and maintaining quality:
Quality Control Step | Description |
Dimensional Inspection | The diameter, thickness, and flatness of each aluminium circle are measured using tools like calipers and micrometers to ensure uniformity and precision in every batch. Consistent dimensions are essential for the functionality and performance of the final product. |
Visual Inspection | Each aluminium circle undergoes a visual inspection to check for surface defects such as scratches, dents, discoloration, or irregularities. This step ensures the aesthetic quality of the circles, which is especially important for applications like cookware and decorative items. |
Mechanical Property Testing | To ensure strength and durability, mechanical tests (e.g., tensile testing, hardness tests, and bending tests) are performed on select aluminium circles. These tests check for properties such as elongation, tensile strength, and hardness, ensuring the material meets specific application requirements. |
Surface Coating Inspection | For aluminium circles that undergo surface treatment (such as anodizing or painting), the uniformity, adhesion, and quality of the coating are thoroughly checked. The goal is to ensure that the coating provides the desired protection or appearance without defects. |
Packaging and Labeling | After passing all quality checks, aluminium circles are carefully packaged in protective materials to prevent damage during transport. Labels indicating key product details such as alloy type, batch number, and diameter are applied to ensure traceability and easy identification. |
Aluminium circle production involves a multi-step quality control process that demands meticulous attention at every stage. Ensuring high standards throughout—from dimensional accuracy and surface inspection to mechanical testing and packaging—is essential for producing reliable, durable aluminium circles that satisfy the requirements of various industries.
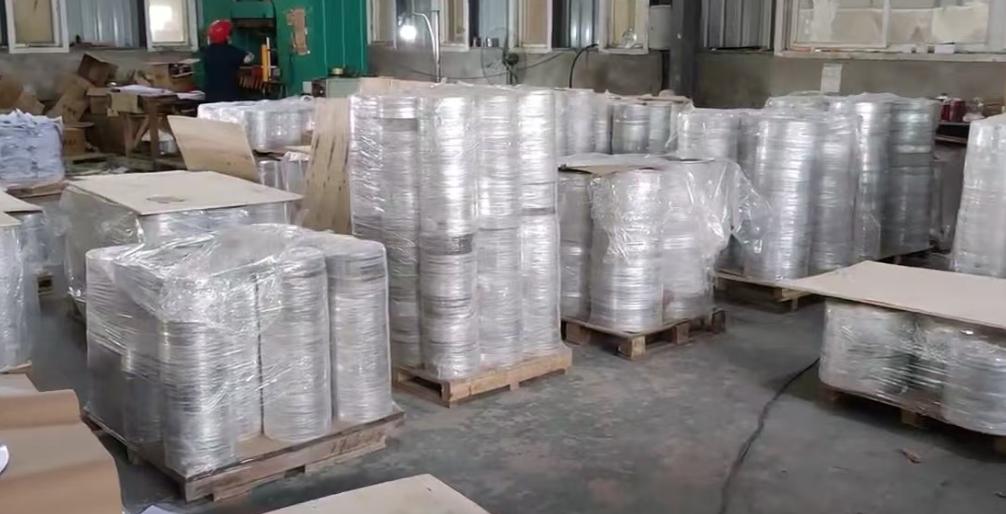
Top Aluminium Circle Manufacturers
The aluminium circle industry is home to several well-established manufacturers that are known for producing high-quality products across various global markets. Here are some of the top players in the field.
The aluminium circle industry is home to several well-established manufacturers that are known for producing high-quality products across various global markets. Here are some of the top players in the field.
- Jinan Huacheng Metal Co., Ltd.: Based in China, Huacheng Metal is a prominent manufacturer specializing in the production of high-quality aluminium circles used in various industries, including cookware, lighting, and electronic components. Renowned for its precision and efficiency, the company has built a solid reputation for delivering durable and dependable products.
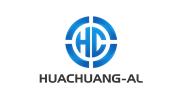
- Aleris (now part of Novelis): A global leader in aluminium rolled products, Aleris manufactures aluminium circles for diverse applications across industries such as automotive, packaging, and industrial sectors. With a strong focus on innovation and sustainability, Aleris has become a well-respected name in the aluminium industry, providing high-performance products to customers around the world.
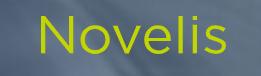
- Lanren Aluminium: A reliable and trusted manufacturer, Lanren Aluminium is known for producing high-quality aluminium circles with precision and consistency. What sets Lanren Aluminium apart is its focus on providing customized solutions tailored to the unique needs of each customer. With advanced production technology, strict quality control, and an emphasis on timely delivery, Lanren Aluminium has gained recognition as a top choice for businesses seeking dependable aluminium circle products.
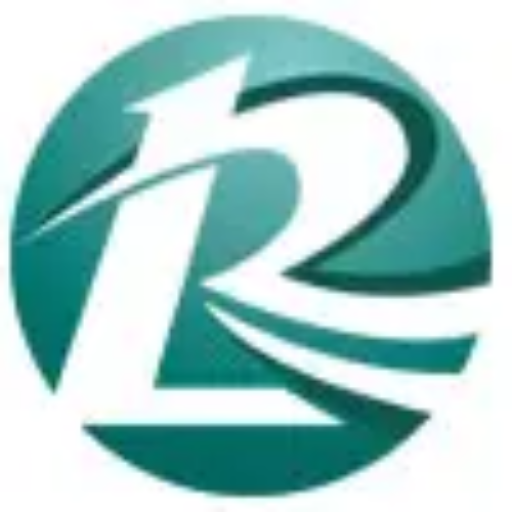
- Chalco: Chalco, one of China’s largest state-owned aluminium producers, has a significant presence in the manufacturing of aluminium circles. Their products are used across a variety of sectors, from cookware to electronics, and they are known for their adherence to strict quality control standards.
These manufacturers are influential figures in the aluminum circle market, renowned for their capacity to meet worldwide demand while upholding exceptional quality standards. Their products are essential in both large-scale production and custom orders, playing a crucial role in the industries they serve.
Invest in Aluminium Circle
If you are looking to purchase aluminium circles or would like to learn more about the manufacturing process and the various applications of these versatile products, feel free to get in touch with us. We are here to provide you with detailed information, help you choose the right aluminium circles for your needs, and offer competitive pricing for bulk purchases. Whether you are a manufacturer, distributor, or simply looking for high-quality aluminium circles for your next project, our team is ready to assist you every step of the way. Contact us today to explore your options and make the best investment in aluminium circles.
Related Products