Common Applications about Anodized Aluminium Circle
Anodized aluminium circles are popularly utilized by various industries due to their durability, corrosion resistance and aesthetic appeal. Anodizing enhances aluminium’s inherent properties making it suitable for applications ranging from cookware to industrial components.
In this article, we’ll take a close look at the key characteristics and applications of anodized aluminium circles as well as why they outshone other materials. Additionally, we will offer tips on selecting anodized aluminium circles suitable for your needs.
Key Properties of Anodized Aluminium Circles
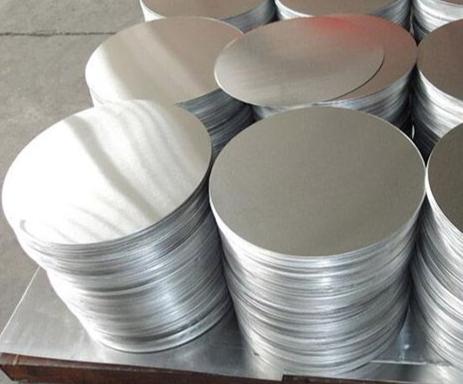
Anodized aluminium circles are highly valued for their superior performance in various industries. Here are the four most important properties that make them a top choice:
- Exceptional Corrosion Resistance – The anodizing process creates a protective oxide layer, making the aluminium resistant to rust, moisture, and chemical exposure, ideal for harsh environments.
- Enhanced Durability & Scratch Resistance – Anodized aluminium is harder than raw aluminium, reducing wear and tear in high-friction applications like cookware and industrial components.
- Heat & Thermal Conductivity – It efficiently distributes heat, making it perfect for cookware, LED lighting, and heat-sensitive applications while maintaining structural integrity.
- Lightweight Yet Strong – Despite being lighter than steel, anodized aluminium retains high strength-to-weight ratios, reducing material costs without sacrificing performance.
These properties ensure longevity, efficiency, and versatility, making anodized aluminium circles a preferred material in industries ranging from kitchenware to aerospace. Whether for durability, aesthetics, or functionality, they outperform many alternatives.
Common Applications of Anodized Aluminium Circles
Anodized aluminium circles are extremely useful and widely employed across multiple industries due to their impressive durability, corrosion resistance, and aesthetic appeal. Anodizing creates a protective oxide layer which enhances the metal’s natural properties, making it suitable for demanding applications. Below we outline their most frequent applications in more depth.
Cookware and Kitchenware
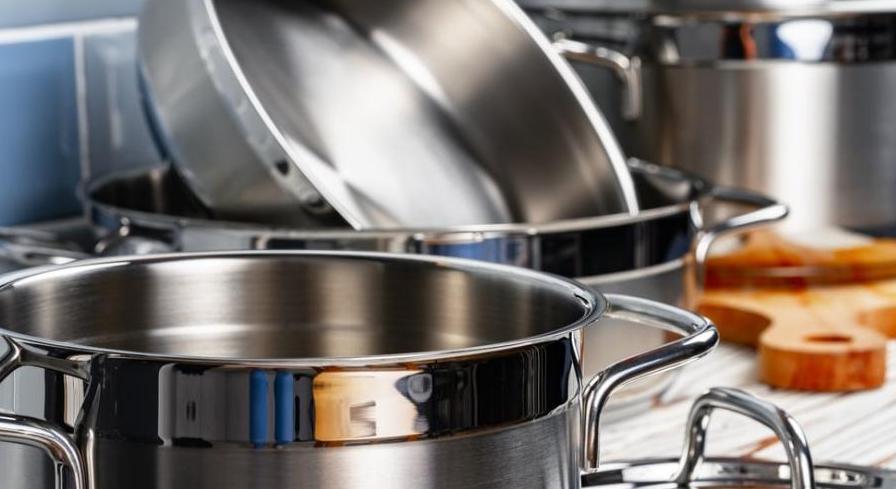
Anodized aluminium circles have become an invaluable addition to cookware applications in recent years. Their superior heat conductivity ensures even cooking while their anodized layer prevents food from sticking, making cleaning simpler. Anodized circles are widely used for manufacturing high-quality pots, pans, baking sheets and pressure cooker lids made with these circles; unlike untreated aluminium it does not react with acidic foods, providing both safety and longevity; additionally their hard surface resists scratches and wear making it the go-to choice both at home as well as commercial kitchens alike.
Signage and Decorative Items
Anodized aluminium circles have become popularly used in signage and decorative applications due to their customizable finishes, making them the ideal solution for branding elements such as nameplates, logos, architectural signage, or interior design accents such as wall panels. Their lightweight nature ensures easy installation, while their resistance against fading and corrosion ensures they retain their appearance over time.
Lighting Industry
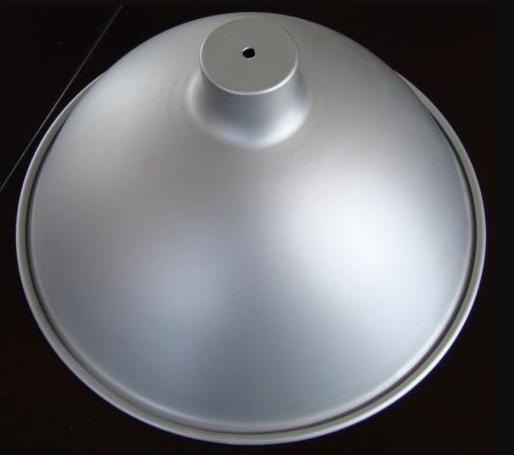
Anodized aluminium circles play a pivotal role in lighting applications, particularly LED and reflector designs. Their reflective properties maximize light output while reducing energy use, making them suitable for LED light reflectors, lamp housings, and streetlight components. Furthermore, anodization enhances heat dissipation to prevent overheating fixtures as well as lengthen their lifespan while remaining weather- and UV degradation resistant to ensure long-term performance in both indoor and outdoor lighting solutions.
Industrial and Automotive Components
Anodized aluminium circles have numerous industrial and automotive uses beyond consumer goods. Thanks to their superior strength-to-weight ratio, anodized aluminium circles are ideal for manufacturing machine parts such as heat sinks and electronic enclosures; in the automotive world, trim pieces, reflectors, and engine components, where corrosion resistance and durability are critical – they’re even used on engine covers! Engineers and manufacturers rely on them as reliable choices due to their ability to withstand harsh environments without degrading, making anodized aluminium circles an invaluable resource when selecting components.
Anodized aluminium circles have quickly become the go-to material in kitchenware, lighting, signage, and industrial applications due to their superior durability, functionality, and aesthetic versatility. Their properties also make them an attractive replacement for untreated aluminium, steel, and plastic in many situations.
Why Use Anodized Aluminium Circles over Other Materials?
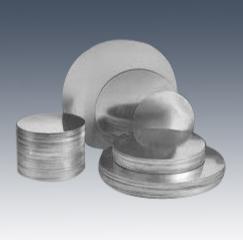
Anodized aluminium circles offer several advantages that make them a superior choice compared to other materials like stainless steel, untreated aluminium, or plastic.
- One of the biggest benefits is enhanced durability—the anodizing process creates a hard, protective oxide layer that resists scratches, corrosion, and wear. Unlike raw aluminium, which can oxidize over time, anodized aluminium maintains its appearance and structural integrity even in harsh environments.
- Another key advantage is lightweight strength. While stainless steel provides durability, it is significantly heavier, increasing transportation and handling costs. Anodized aluminium, on the other hand, offers similar strength at a fraction of the weight, making it ideal for applications where weight reduction is crucial, such as in aerospace, automotive, and portable cookware.
- Anodized aluminium also excels in heat and electrical conductivity, making it perfect for lighting, electronics, and cookware. Unlike plastic, which can melt or degrade under high temperatures, anodized aluminium withstands extreme heat while efficiently dissipating it. Additionally, the anodized layer provides excellent color retention, allowing for vibrant, long-lasting finishes that won’t fade or peel like painted surfaces.
- Finally, anodized aluminium is eco-friendly—it is fully recyclable, and the anodizing process itself is non-toxic, unlike some coating methods used on other metals. When considering cost, performance, and sustainability, anodized aluminium circles are often the best choice for both industrial and consumer applications.
How to Choose the Best Anodized Aluminium Circle
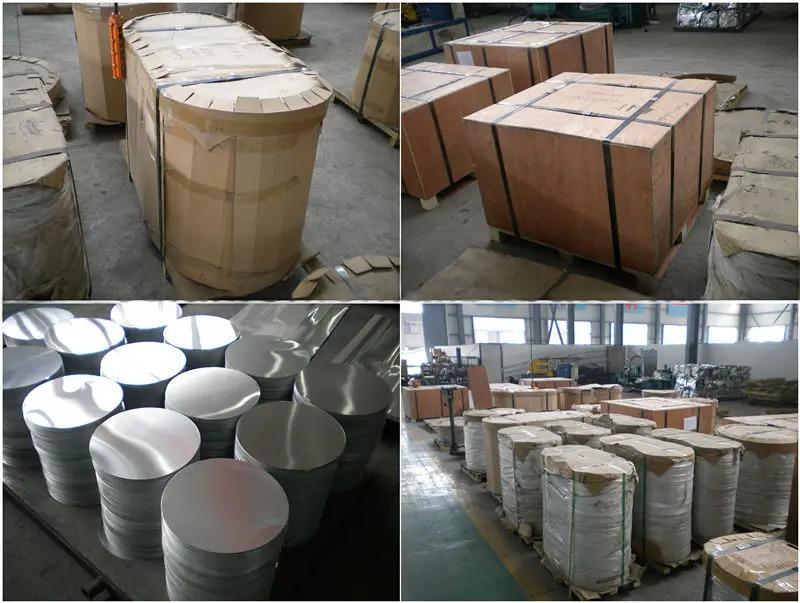
Selecting an anodized aluminium circle that meets all your project requirements will ensure long-term durability and efficiency for any given task. Here are a few things you should keep in mind when making this selection:
- Thickness & Diameter – Thick discs (2 mm to 6 mm) are best suited to heavier-duty applications like cookware, while thinner ones work as lighting reflectors.
- Alloy Grade – Common alloy grades such as 1050 (soft and formable) and 3003 (stronger and corrosion-resistant) cater to various requirements for various tasks.
- Anodizing Quality – To optimize corrosion resistance, choose an anodized coating with uniform, pore-free coverage; avoid uneven or peeling surfaces.
- Finish & Color Options – Select matte, glossy or colored finishes according to aesthetic considerations (e.g. signage vs. industrial parts).
Partner with experts such as Lanren, an anodized aluminium circle supplier with ISO-certified production, stringent quality controls, and customized solutions that offer maximum value to their clients.
Lanren offers tailored anodized aluminium circles at consistently competitive pricing to meet all of your cooking, lighting, and other needs. Reach out now for a quote!
Related Products