Choosing Between Raw and Finished Aluminum Disks for Your Project
Aluminum disks are a popular choice in various industries, from automotive and aerospace to household appliances and construction. When selecting aluminum disks for your project, you may find yourself deciding between raw and finished options. This guide will help you understand the differences, benefits, and considerations to make an informed choice.
What Are Raw Aluminum Disks and Finished Aluminum Disks?
Raw Aluminum Disks
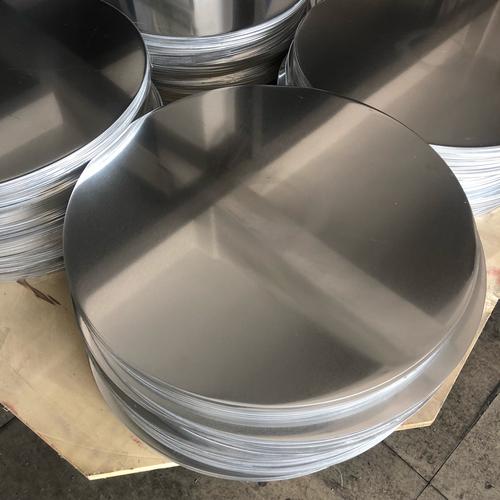
Raw aluminum disks are unprocessed aluminum sheets or rounds that have been shaped into a disk form but have not undergone further refinement or finishing. These disks are in their most basic state and are characterized by the following features:
- Untreated Surfaces: Raw aluminum disks typically have rough surfaces that may display marks from cutting, stamping, or extrusion. They lack polish or coatings, and their edges are often sharp.
- Highly Customizable: In their basic form, raw aluminum disks are ideal for machining, polishing, or other modifications. They serve as a versatile starting point for projects requiring intricate designs or specialized finishes.
- Manufacturing Flexibility: These disks are well-suited for applications requiring precise, tailored specifications. Their adaptability makes them a popular choice for custom machining, drilling, and other alterations in various industries and DIY projects.
- Common Uses: Raw aluminum disks are widely used in aerospace, automotive, and manufacturing sectors. They are often employed for prototyping, creating custom parts, or serving as materials for additional finishing processes.
Finished Aluminum Disks
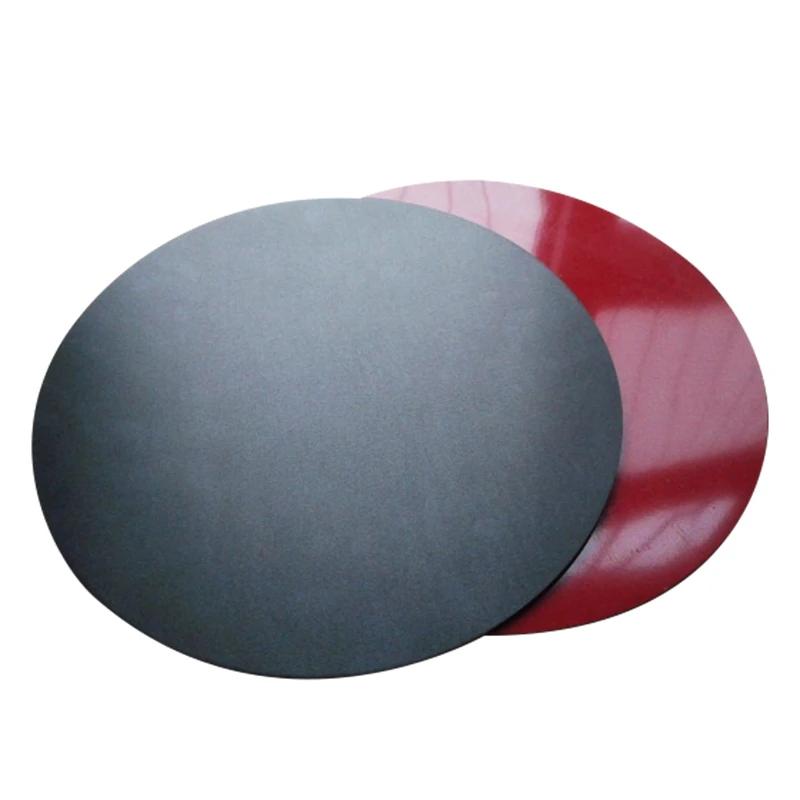
Finished aluminum disks, in contrast, have undergone specific processes to improve their properties, appearance, and functionality, making them ready for immediate use, such as coated aluminum disks, mill finished aluminum disks . These disks typically feature:
- Polished and Smooth Surfaces: Finished aluminum disks often have surfaces that are polished, anodized, or coated for a smooth, visually appealing finish. The edges are usually rounded or deburred for both safety and enhanced aesthetics.
- Pre-Processed Features: These disks may be anodized for added corrosion resistance, coated for greater durability, or painted for a decorative look. Such treatments ensure the disks are not only functional but also possess a professional appearance and can withstand environmental factors.
- Consistency and Precision: Due to their pre-processed nature, finished aluminum disks provide uniformity in size, shape, and appearance. This makes them well-suited for applications that demand high precision, such as those in the automotive, consumer electronics, and architectural sectors.
- Common Uses: Finished aluminum disks are extensively used in industries where aesthetics, durability, and immediate availability are crucial. They are often found in applications such as decorative elements, automotive components, electrical enclosures, and other products that require minimal or no further modification.
Raw Aluminum Disks vs. Finished Aluminum Disks
The choice between raw and finished aluminum disks depends on various factors, such as cost, project specifications, and the degree of customization required. Below is a comprehensive comparison of raw and finished aluminum disks across key criteria to help you determine which option best meets your needs:
Aspect | Raw Aluminum Disks | Finished Aluminum Disks |
Cost | Raw aluminum disks are typically more affordable as they require minimal processing, making them a cost-effective option for those on a budget. | Finished disks are more expensive due to the additional treatments, coatings, or machining they undergo. |
Processing | Raw disks require further processing, such as machining, polishing, or coating, to meet specific project needs. They offer flexibility but demand more time and resources. | Finished disks come pre-processed and ready for use. Their surface treatments or precision machining are done during production, saving time during implementation. |
Customization | Raw disks offer high customization potential, allowing for modifications in shape, size, and surface treatment, depending on the project requirements. | Finished disks offer limited customization since they come with pre-existing surface finishes and dimensions. Customization is more challenging after the disk is processed. |
Durability | Raw aluminum disks may require additional treatments (e.g., anodizing or coating) to improve their durability and resistance to corrosion. | Finished disks often have enhanced durability with built-in protective coatings or anodizing, making them more resistant to environmental wear. |
Appearance | Raw aluminum disks typically have a plain, industrial appearance, suitable for applications where aesthetics are not the primary concern. | Finished disks come with polished, anodized, or powder-coated surfaces, making them more visually appealing for projects where aesthetics matter. |
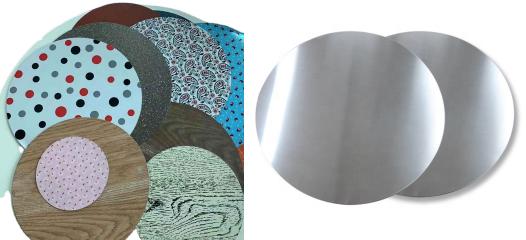
What to Consider When Choosing Between Two?
Choosing between raw and finished aluminum disks comes down to a few important factors that will impact your project. Here’s what you should think about:
Choosing between raw and finished aluminum disks comes down to a few important factors that will impact your project. Here’s what you should think about:
- What You Really Need: Start by considering the specific requirements of your project. If you plan to do extensive custom work, such as machining, cutting, or welding, raw aluminum disks offer the flexibility to be shaped as needed. However, if you need a product that’s ready for use with minimal additional work, finished disks will save you time and effort.
- Your Budget: Raw aluminum disks are typically more affordable since they undergo little to no processing. However, if you intend to invest time in processes like polishing or applying protective coatings, costs can accumulate quickly. Finished disks have a higher upfront cost, but they may prove more cost-effective in the long term when you factor in the time and resources saved by avoiding additional work. Consider your budget and whether the convenience of finished disks justifies the higher price.
- Durability and Protection: If your disk is going to be exposed to harsh conditions, like outdoor elements or corrosive environments, finished disks may be a better option. Processes like anodizing or powder coating offer extra protection and extend the life of the material. Raw disks won’t have this built-in protection, so you’d need to treat or coat them afterward if needed, which adds time and cost.
- How It Looks: If the aluminum disk is going to be part of a visible product—maybe for a consumer item or a design piece—you’ll likely want it to look polished and professional. Finished aluminum disks come ready with a sleek, clean surface that gives a high-quality finish. Raw disks have more of an industrial look and might need extra work to meet aesthetic standards.
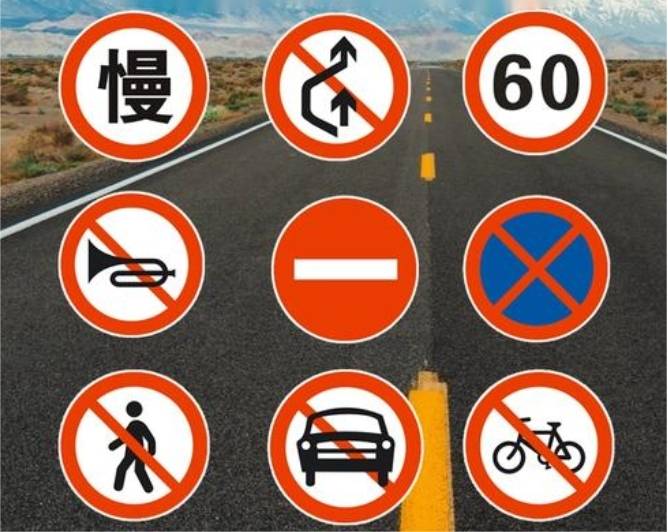
- Time: Lastly, consider your project timeline. If you’re working under a tight deadline, finished disks are a better option as they are ready for immediate use. Raw disks, on the other hand, may require extra time for adjustments or treatments, potentially causing delays.
By weighing these factors, you can make an informed decision based on what’s most important for your project, whether it’s cost, time, appearance, or durability.
To Sum Up
Raw aluminum disks offer more flexibility and are cost-effective, making them a great choice for projects that require customization or further processing. On the other hand, finished aluminum disks save time and effort, offering enhanced durability and a polished look, which makes them ideal for projects where quick turnaround, performance, and aesthetics are essential.
By weighing the pros and cons of each option and aligning them with your project goals, you can make a well-informed decision. Whether you need the adaptability of raw aluminum disks or the ready-to-use features of finished ones, selecting the right manufacturer will ensure the success and efficiency of your project. If you are looking for a reliable aluminum disk supplier, Lanren will be your first choice. Contact us to learn more information!
Related Products