Aluminum Disks vs. Steel: A Comparative Analysis
The choice between aluminum and steel has been a key consideration for manufacturers across various industries. While steel has a reputation for strength and durability, aluminum disks often take the lead in performance, thanks to their unique material properties.
Material Properties of Aluminum Disks and Steel
The properties of aluminum and steel materials play an important role in determining whether they are suitable for a certain application.
Aluminum Disks
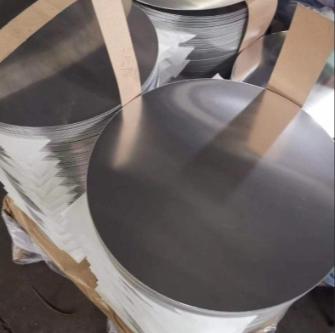
Aluminum is favored for its light weight and corrosion resistance. Its main properties include:
- Lightweight and Corrosion-Resistant: Aluminum is about one-third the weight of steel and naturally forms a protective oxide layer, preventing rust without the need for additional coatings.
- Good Thermal Conductivity and Workability: Aluminum efficiently dissipates heat and is easy to shape, making it ideal for applications that require thermal management or complex designs.
- Sustainable: Aluminum is highly recyclable, retaining its properties even after multiple recycling cycles, making it an environmentally friendly choice.
Steel Disks
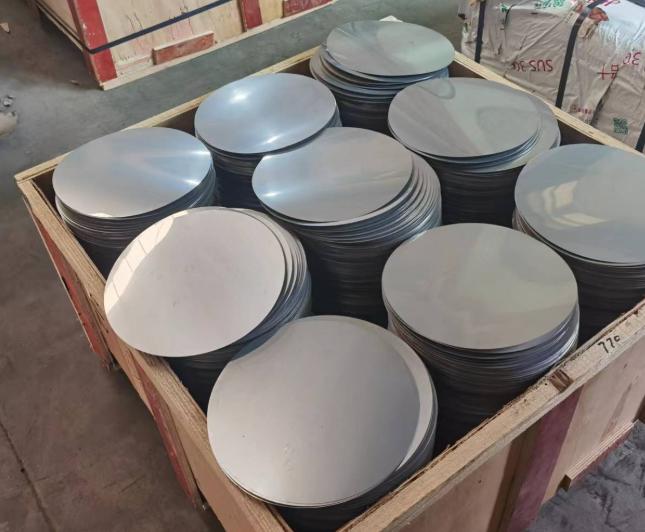
Steel is renowned for its strength and durability, making it a critical material for heavy-duty applications. Its key properties include:
- High Strength and Durability: Steel excels in withstanding significant stress and heavy loads, providing superior structural integrity and long-lasting performance, even in demanding environments.
- Lower Thermal Conductivity and Heavier Weight: Compared to aluminum, steel has lower heat transfer capabilities and is notably heavier, which can be a drawback in applications where weight is a concern.
- Corrosion Susceptibility: Steel is prone to rust and requires protective treatments, such as galvanization, to prevent corrosion, especially in outdoor or marine settings.
Comparative Analysis: Aluminum Disks vs Steel
When comparing aluminum disks to steel, the key differences lie in weight, strength, corrosion resistance, heat conductivity, and manufacturing ease. Below is a brief summary of how aluminum and steel stack up across these factors:
Property | Aluminum Disks | Steel |
Weight | Lightweight, about one-third the density of steel | Heavier, higher density |
Corrosion Resistance | Naturally corrosion-resistant, no coatings needed | Prone to rust, requires treatments like galvanization |
Thermal Conductivity | High, ideal for heat dissipation | Low, less effective in heat-sensitive applications |
Strength | Good strength-to-weight ratio, but less strong than steel | High strength, ideal for heavy-duty applications |
Manufacturing | Easy to shape, cut, and form | Harder to machine, more rigid |
This table highlights the main differences, with aluminum disks excelling in weight, corrosion resistance, and thermal performance, while steel disks are favored for their strength and durability in heavy-duty applications.
Main Industry Applications of Aluminum Disks and Steel Disks
Industry | Aluminum Discs | Steel Discs |
Aerospace | Lightweight components such as turbine blades, disk brakes | – |
Automotive | Wheels, brake rotors, engine parts | Brake rotors, flywheels, engine components |
Electronics & Electrical | Heat sinks, enclosures, power supplies | – |
Packaging | Cans, foils, and containers | – |
Renewable Energy | Solar panel frames | – |
Industrial Machinery | – | Gears, bearings, flywheels, other high-stress components |
Heavy Equipment | – | Excavators, bulldozers, tractors |
Defense & Military | – | Armor plating, weapon systems |
Energy & Power Generation | – | Turbines, generators, power plant components |
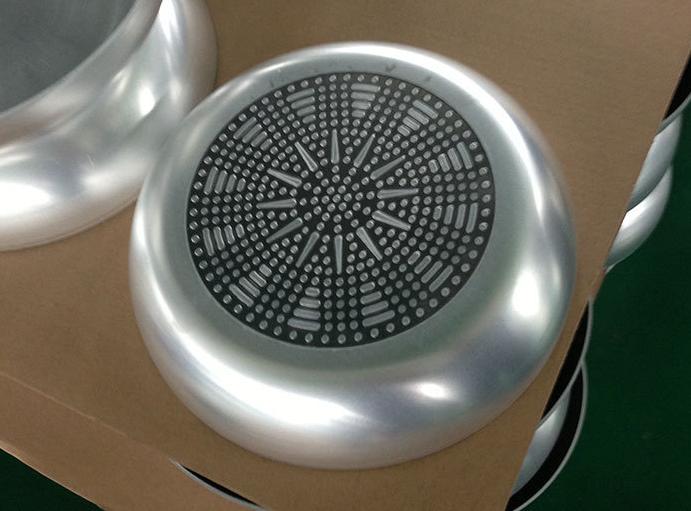
- Aluminum discs are primarily used in industries where lightweight, corrosion-resistant, and thermally conductive materials are required. Key applications include aerospace components, automotive parts like wheels and brake rotors, electronics for heat management, packaging, and renewable energy systems like solar panel frames.
- On the other hand, steel discs are essential in industries demanding strength, durability, and resistance to mechanical stress. They are widely used in heavy machinery manufacturing, automotive components, heavy equipment, defense systems, and power generation, where high tensile strength and toughness are crucial for performance and reliability.
While aluminum discs excel in lightweight applications, steel discs dominate in heavy-duty environments where performance under stress is required.
How to Choose Between Aluminum Disks and Steel Disks?
When deciding between aluminum and steel disks, it’s important to consider specific factors that affect the performance, cost, and durability of the material. Below are four key points to guide your decision-making process:
Weight Considerations
- Aluminum is significantly lighter than steel. This is one of its most notable advantages, particularly for applications where reducing weight is crucial.
- Automotive & Aerospace: In industries like automotive and aerospace, lighter materials contribute to better fuel efficiency, enhanced performance, and reduced energy consumption. Aluminum’s lower weight can also improve handling and speed in these industries.
- Electronics: For devices like laptops, smartphones, and drones, lightweight components are essential for portability and ease of use.
- General Use: If your application involves components that need to be moved, transported, or manipulated frequently, choosing aluminum can result in a much easier and cost-effective process.
- Steel is much heavier, which makes it more suitable for heavy-duty applications where weight is less of a concern.
- Structural Support: Steel is ideal for structural components like beams, columns, and heavy machinery where strength and rigidity are far more important than weight.
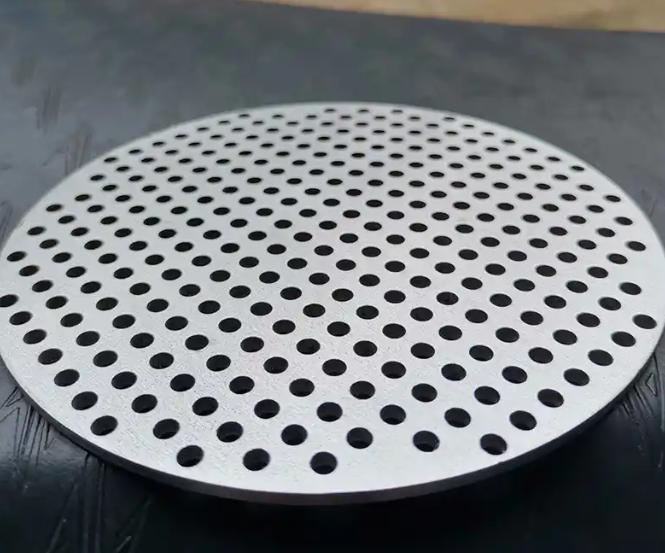
Corrosion Resistance
- Aluminum’s Natural Resistance: One of the standout features of aluminum is its ability to naturally resist corrosion. Aluminum forms a protective oxide layer when exposed to air, preventing rust and degradation. This makes aluminum disks the ideal choice for marine applications, outdoor products, and harsh environments like chemical plants.
- Steel’s Vulnerability: Steel, on the other hand, is highly susceptible to corrosion, especially when exposed to moisture, salt, or other corrosive substances. While it is possible to coat steel with protective layers (e.g., galvanization), it will still require regular maintenance to ensure its longevity, which can add to long-term costs.
- Lower Maintenance with Aluminum: The inherent corrosion resistance of aluminum means fewer maintenance requirements and longer product lifespans, making it an excellent choice for products where longevity is important.
Strength and Durability
- Steel’s Superior Strength: Steel is known for its superior tensile strength and durability, making it the material of choice when strength is a top priority. In industries such as construction, heavy machinery, and defense, steel’s ability to handle heavy loads and endure extreme conditions is essential for ensuring structural integrity and reliability.
- Aluminum’s Strength-to-Weight Ratio: Although aluminum doesn’t match steel in raw strength, its remarkable strength-to-weight ratio makes it an ideal choice for many applications. When weight reduction is a critical factor, such as in automotive wheels or aircraft components, aluminum provides a balanced solution, offering both sufficient strength and reduced mass for enhanced performance and efficiency.
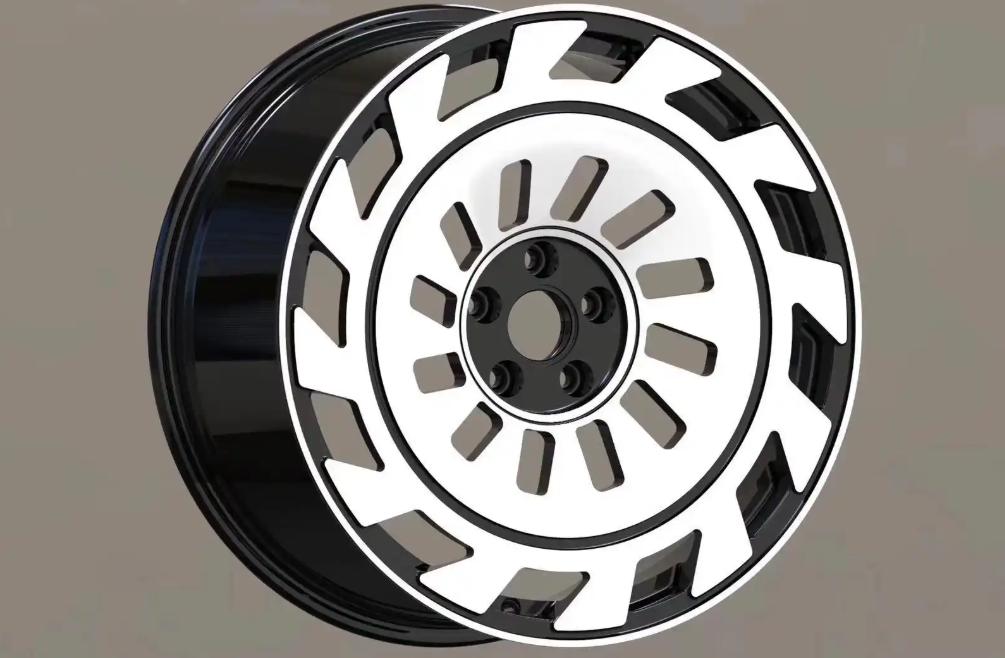
For applications that demand high load-bearing capacity or structural strength, steel is the clear choice. However, when performance or efficiency depends on minimizing weight, aluminum is often the better option, delivering the necessary strength without the added bulk.
Manufacturing and Cost
- Cost-Effectiveness: Steel is typically less expensive to produce and purchase compared to aluminum, making it a more cost-effective option for applications where budget is a primary consideration. For large-scale projects or mass production where minimizing upfront costs is essential, steel is often the more economical choice.
- Ease of Manufacturing with Aluminum: Aluminum is easier to machine, shape, and form than steel, which simplifies the manufacturing process and can reduce production costs. Its malleability allows for more intricate or customized designs, while also requiring less energy and time to process, making it a more efficient material for complex projects.
- Long-Term Savings: Although aluminum has a higher initial cost than steel, its lightweight nature and resistance to corrosion can result in significant long-term savings, particularly in industries where maintenance and durability are critical. Additionally, aluminum’s recyclability enhances its sustainability, further reducing costs over the product’s lifecycle.
All in all, choosing between aluminum and steel disks depends on your needs. Aluminum is ideal for lightweight, corrosion-resistant applications in industries like aerospace and automotive, while steel offers greater strength and durability for heavy-duty uses in construction and machinery. Consider factors like weight, strength, and corrosion resistance to select the right material for your project, ensuring the best performance and cost-efficiency.
Need more information about aluminum disks? We are glad to answer your questions. Just free free to contact us.
Related Products