Aluminium Circle Surface Treatments: Which Finish is Fit for Your Application
Aluminium circles, which are widely used in a variety of industries such as cookware, lighting, and signage, require specialized surface treatments to improve their qualities and compatibility for varied applications. The surface treatment of aluminium circles is critical for increasing durability, corrosion resistance, aesthetic appearance, and performance. In this post, we’ll look at the most prevalent aluminium circle surface treatments, variables to consider when selecting a surface finish, and how to match them to your specific application.
Common Aluminium Circle Surface Treatments
Aluminium circles can be treated with various surface finishes, each offering distinct benefits for different purposes. These treatments can improve properties such as corrosion resistance, hardness, and visual appeal. Let’s dive into the three main categories of aluminium surface treatments:
Chemical Finishes
Chemical finishes involve the use of chemical processes to alter the surface properties of aluminium circles. These treatments are often used to improve corrosion resistance, enhance adhesion for further coatings, or achieve a specific aesthetic look.
Anodizing: Anodizing is one of the most used chemical treatments for aluminum. It uses an electrochemical method to form a thick, protective oxide layer on the surface. This coating not only increases corrosion and wear resistance, but it also adds a decorative finish. Because of its durability and aesthetic adaptability, anodized aluminum circles are widely utilized in architectural applications, automotive components, and consumer electronics.
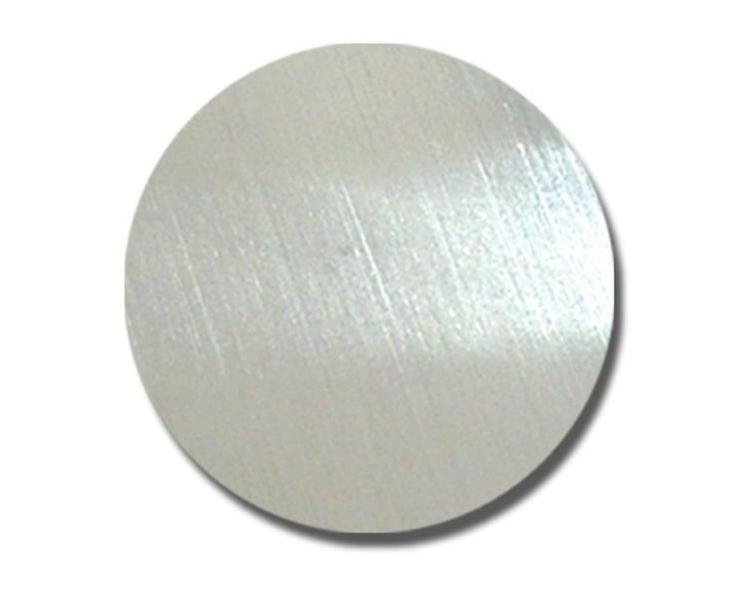
Chromate Conversion Coating: This treatment involves applying a chromate-based layer to the aluminium surface, which improves corrosion resistance and provides an excellent base for paint adhesion. Chromate conversion coatings are commonly used in aerospace, military, and marine applications due to their ability to withstand harsh environments.
Chemical Etching: Chemical etching is a process that uses acidic or alkaline solutions to remove a thin coating of aluminum surface. This method produces a smooth, matte finish that is suitable for prepping a surface for painting, printing, or bonding. It is widely utilized in areas that require precise surface uniformity, such as electronics and signage.
Mechanical Finishes
Mechanical finishes involve physical methods to alter the aluminium circle surface. These finishes are primarily used to enhance the appearance or provide specific properties like smoothness or texture. The most common mechanical treatments include:
Polishing: Polishing is a procedure that smoothes the surface of aluminum to produce a glossy, reflective finish. This treatment is appropriate for applications where appearance is important, such as ornamental objects, consumer goods, and kitchenware.
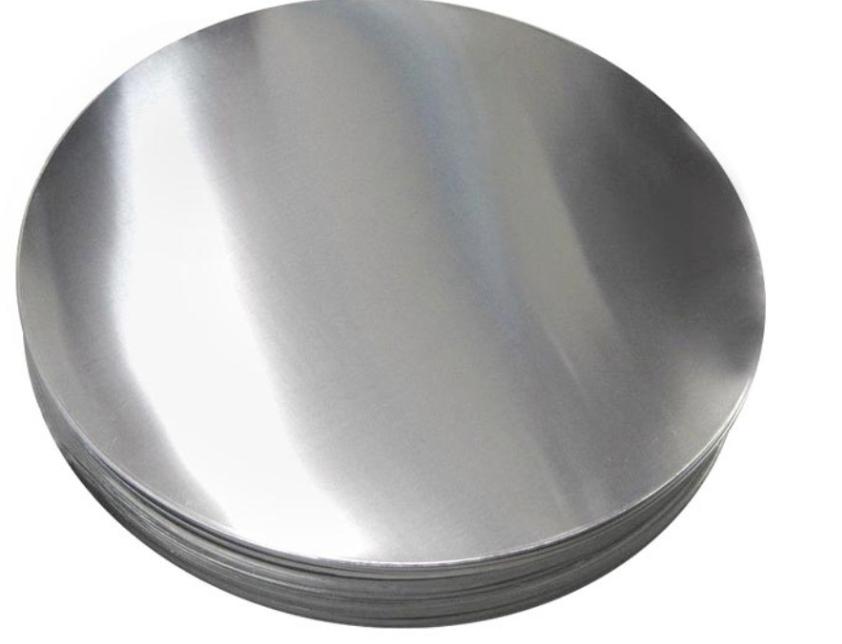
Grinding: Grinding is typically used to smooth out rough surfaces or remove surface defects. It provides a more uniform and precise surface, which is essential in applications that require high tolerance levels and smooth finishes.
Brushing: Brushing creates a consistent, rough surface on aluminum. The procedure involves applying a fine texture to the surface with abrasive brushes or pads, resulting in a matte or satin finish. It is widely used for aesthetic objectives in architecture and interior design.
Coatings
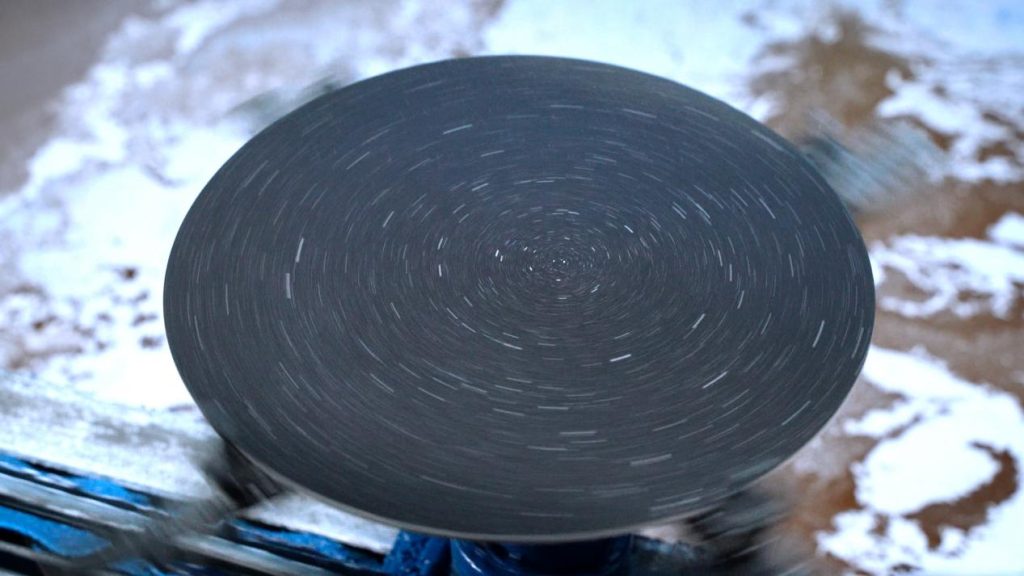
Coatings are applied to the aluminium circle surface to provide additional protection, enhance appearance, or add functional properties. These finishes can be organic (e.g., paint) or inorganic (e.g., ceramic).
PVDF Coating: Polyvinylidene fluoride (PVDF) coatings are well-known for their high durability and resistance to UV radiation, chemicals, and weathering. These coatings are commonly employed in architectural applications such as building facades and roofing, where long-term performance is essential.
Powder Coating: A dry powder is applied to the aluminum surface and then cured under heat to form a hard, protective layer. This coating has great corrosion resistance, UV resistance, and a variety of color possibilities. It is widely employed in exterior applications, including automotive parts, signs, and architectural features.
Paint Coating: Paint coatings provide both protection and aesthetic appeal. They are available in various colors and finishes, making them suitable for consumer goods, electronics, and architectural applications. Paint coatings are often used when a specific color or design is required.
Factors to Consider When Choosing a Aluminium Circle Surface Treatment
Choosing the right surface treatment for aluminium circles is an important decision that affects their performance, durability, and appropriateness for particular applications. To ensure you choose the proper finish, examine the following critical factors:
- Application Requirement
Begin by understanding the purpose of the aluminium circle. Will it be subjected to extreme circumstances, require electrical conductivity, or have to fulfill certain aesthetic requirements? Surface treatments are required for various purposes, so choose one that meets the project’s functional and visual needs.
- Corrosion resistance
If the aluminium circular will be utilized in locations with moisture, chemicals, or extreme weather, prioritize corrosion-resistant treatments. Anodizing, chromate conversion coating, and powder coating are all great options for preventing rust and degradation.
- Aesthetic Appeal
For applications where appearance is important, such as consumer goods, architectural elements, or decorative items, choose finishes that enhance visual appeal. Polishing, brushing, or powder coating can provide a sleek, attractive finish in a variety of colors and textures.
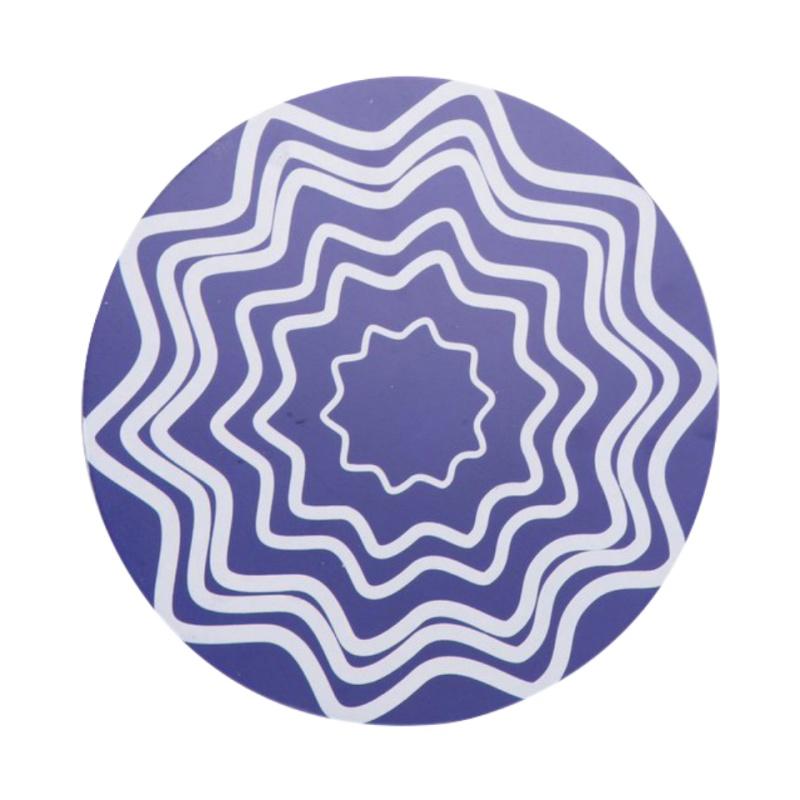
- Adhesion for Further Processing
If the aluminium circle undergoes additional processes, such as painting or printing, select a surface treatment that promotes strong adhesion. Chemical etching or chromate conversion coating, for example, can prepare the surface for subsequent coatings.
- Maintenance Requirements
Consider the long-term maintenance needs of the finish. Some treatments, like anodizing or powder coating, are low-maintenance and resistant to fading, chipping, or scratching, making them ideal for applications where frequent upkeep is not feasible.
By carefully evaluating these factors, you can select the most appropriate surface treatment for your aluminium circles, ensuring they meet the specific demands of your application while delivering optimal performance and longevity.
Matching Aluminium Circle Surface Treatments to Applications
Selecting the appropriate surface treatment for aluminium circles depends on the specific demands of the application. Below is a breakdown of common applications and the surface treatments most suitable for each:
Application | Surface Treatment(s) | Reason for Choice |
Cookware | Anodizing, Powder Coating | Provides heat resistance, non-stick properties, and easy cleaning. |
Automotive Parts | Anodizing, Polishing | Enhances corrosion resistance for outdoor exposure, improves aesthetic appeal. |
Architectural Components | Powder Coating, Anodizing | Offers UV protection, long-lasting durability, and a polished appearance. |
Industrial Equipment | Anodizing, Brushing | Increases durability, resistance to wear and tear, and ease of maintenance. |
Consumer Goods (e.g., Appliances) | Polishing, Powder Coating | Achieves a high-gloss finish, improves visual appeal and scratch resistance. |
Electrical Enclosures | Chromating, Powder Coating | Enhances corrosion resistance and provides an attractive, protective finish. |
Signage | Anodizing, Powder Coating | Durable and weather-resistant, with customizable aesthetics. |
How to Choose the Right Aluminium Circle Finish for Your Application
Choosing the proper finish for your aluminum circle is an important decision that will have a direct impact on the performance, durability, and aesthetics of your product. Here’s a step-by-step guide to help you make the right decision:
- Define Your Primary Needs
Start by considering the most important factors for your application. Is corrosion resistance your top priority? Or is surface aesthetics (such as a polished look) more important? For example:
- If you need extra protection against harsh environmental factors, anodizing or powder coating might be your best option.
- If a glossy, smooth finish is essential for visual appeal, then polishing or brushing could be the way to go.
- Evaluate Environmental Exposure
Where will the aluminum circle be used? Environmental circumstances have an important impact in determining the finish.
- Outdoor applications that are exposed to moisture, humidity, or UV radiation (such as architectural features) benefit from finishes such as anodizing or powder coating.
- Mechanical treatments (such as polishing or brushing) may be sufficient for products that will be utilized in dry, controlled settings, as they focus on appearance rather than corrosion protection.
- Consider Durability and Wear Resistance
If your aluminium circles will undergo frequent handling, friction, or exposure to heavy loads, durability is a critical factor. In these cases:
- Anodizing is highly recommended because it increases the surface hardness and improves wear resistance.
- For applications where a rougher surface is acceptable, brushing may provide the right balance of texture and durability.
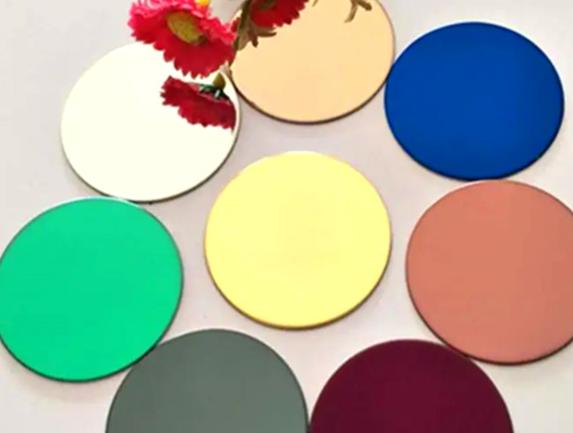
- Aesthetic Considerations
The appearance of your aluminum circles may be critical, particularly in consumer-facing items or high-visibility applications. If beauty matters:
- Polishing produces a bright, mirror-like surface that adds a high-end appeal to ornamental objects, kitchenware, and automobile components.
- Brushing creates a more subdued, matte texture, which is ideal for modern designs or architectural finishes.
- Evaluate Maintenance and Longevity
Consider how much maintenance your aluminum circles will need over time.
- Powder coating is a low-maintenance and long-lasting finish that resists wear and is easy to clean.
- Anodized finishes also provide long-term protection with little maintenance, particularly in settings where moisture and chemicals are widespread.
- Consult an Aluminium Circle Manufacturer
If you’re uncertain about which finish best suits your application, it’s a good idea to consult directly with an aluminium circle manufacturer. They can provide expert advice tailored to your specific needs, such as recommending the most suitable surface treatment based on the product’s function, durability requirements, and aesthetic preferences. A manufacturer will also be able to offer insights into the latest finishes and help you select the right treatment to ensure optimal performance and longevity.
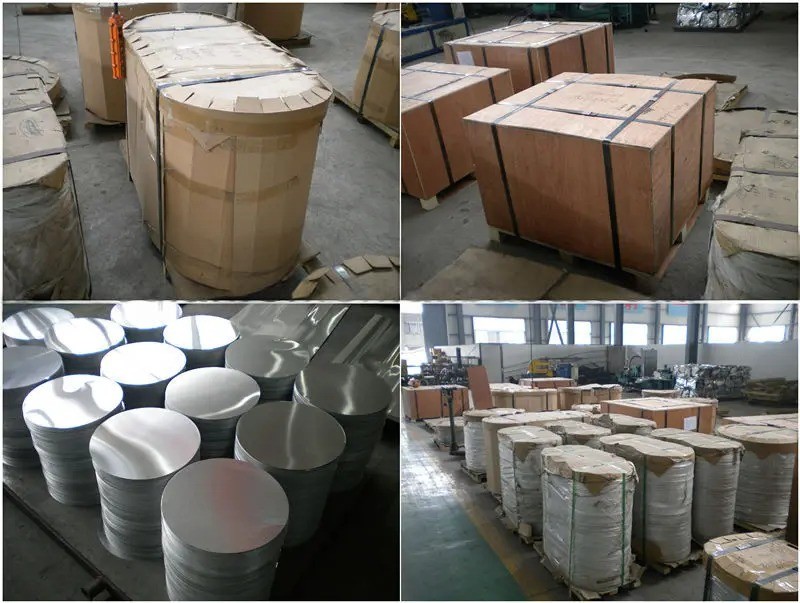
The surface treatment of aluminium circles is a critical factor in determining their performance, durability, and suitability for specific applications. By understanding the different types of finishes—chemical, mechanical, and coatings—and considering factors such as application requirements, corrosion resistance, and cost, you can select the right treatment for your needs.
If you are interested in investing in aluminium circles, please feel free to contact us!
Related Products